Achieving Precise Polishing for Architectural Stone Details
In the world of architecture, the beauty of stone is timeless. From grand facades to intricate details, stone has been a symbol of strength and elegance for centuries. But to achieve the perfect finish that highlights its natural beauty and craftsmanship, precise polishing is essential. Whether it’s a sleek modern design or a classical masterpiece, the art of stone polishing plays a crucial role in elevating the overall aesthetic and longevity of architectural features. So, what makes a perfect stone polish, and how do architects and craftsmen achieve such a high level of precision?
First, it’s important to understand that stone, in its raw form, is rarely suited for the refined beauty that we often associate with polished surfaces. Granite, marble, limestone, and other types of stone may have the inherent qualities to shine, but to reveal their true luster, a detailed polishing process is necessary. A polished stone surface can showcase its rich texture, depth of color, and intricate veins, adding a touch of sophistication to any building or interior.
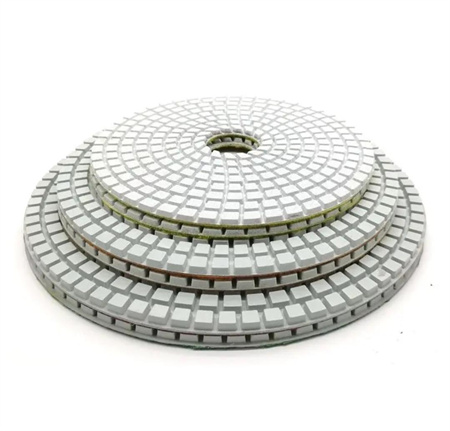
But achieving precision in polishing requires more than just the right tools—it demands skill, experience, and an understanding of the stone’s unique properties. The natural variations in texture, color, and hardness of different stones can make the polishing process more challenging than it appears. For example, marble, with its soft surface, requires careful handling to avoid scratches, while granite, being much harder, demands specialized equipment and techniques to achieve a smooth, reflective finish. Each type of stone requires a tailored approach to bring out the best in its appearance.
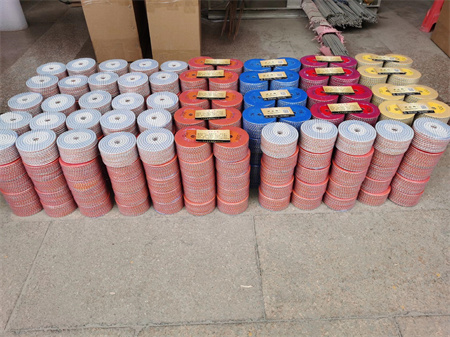
One of the most critical aspects of stone polishing is selecting the right abrasives and polishing compounds. In the early stages, coarse abrasives are used to remove any rough edges, imperfections, or stains on the stone’s surface. As the process progresses, finer abrasives are introduced to smooth the surface further, gradually bringing out the stone’s inherent gloss. Polishing compounds, often in the form of powders or pastes, are then applied to enhance the stone’s sheen. This step is where the true magic happens—when the stone transforms from a dull, unpolished state into a shining, mirror-like surface.
The process is not only about achieving aesthetic beauty but also about functionality. A finely polished stone surface resists dirt, moisture, and other environmental factors that can cause damage over time. This durability ensures that the stone maintains its visual appeal and structural integrity for years to come. In high-traffic areas, such as public buildings or commercial spaces, precision polishing is especially important, as the stone needs to withstand constant wear while retaining its pristine appearance.
In recent years, advancements in technology have significantly improved the precision of stone polishing. Automated machinery, for example, allows for more consistent results across large surfaces, and laser-guided equipment ensures an even finish, even on intricate details. However, while technology has enhanced the speed and efficiency of the process, human craftsmanship remains at the core of achieving the perfect finish. Skilled artisans still play a pivotal role in ensuring the stone is polished to perfection, particularly when dealing with custom or intricate architectural details.
When it comes to architectural stone details—whether it’s a carved column, a decorative arch, or a finely detailed mosaic—the precision of polishing is even more crucial. These elements require meticulous attention to detail, as they often involve complex shapes and intricate designs. The polishing process needs to be carried out in a way that enhances the sculptural aspects of the stone while maintaining the integrity of the design. The polishing must highlight the unique features of the stone without overpowering the craftsmanship or losing the texture that makes each piece distinct.
The use of precise polishing extends beyond the aesthetics of the stone. It plays a vital role in preserving the stone for generations. Stone, being a natural material, is susceptible to weathering, discoloration, and erosion over time. A well-polished surface acts as a protective barrier, shielding the stone from the elements and reducing the wear and tear that can result from exposure to sunlight, moisture, or pollutants.
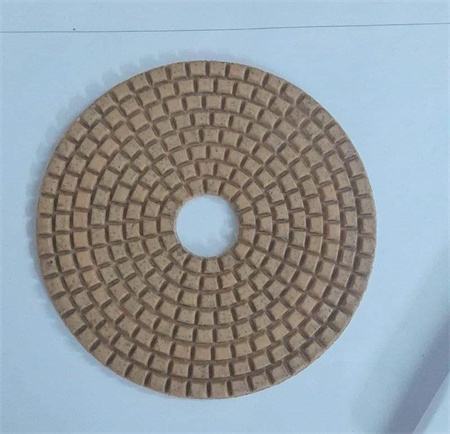
Architectural stone details often become the focal points of a building or space, drawing the eyes of visitors and leaving a lasting impression. When polished with precision, these details not only serve as decorative elements but also as testaments to the skill and dedication of the craftsmen who worked on them. The beauty of architectural stone polishing lies not only in its visual appeal but in the timelessness it imparts to the structure, transforming simple stone into a work of art that will be admired for years, if not centuries.
As the demand for custom and intricate stonework continues to rise in the field of architecture, the art of precise polishing will only grow in importance. It’s a process that combines tradition with innovation, allowing for the creation of architectural masterpieces that stand the test of time. The next time you admire a stunning stone detail on a building, remember that it’s not just the design that makes it exceptional—it’s the craftsmanship and precision of the polishing process that brings it to life.