Low-Cost Polishing Pads That Don’t Sacrifice Quality
When it comes to car detailing or any other polishing projects, the right polishing pad can make all the difference. High-end pads often come with a hefty price tag, leaving some to wonder if it’s possible to get professional-grade results without breaking the bank. The good news is, you can! Low-cost polishing pads that don’t compromise on quality are not only a reality but can deliver fantastic results at a fraction of the cost.
The myth that you need to spend a fortune for top-notch polishing performance is just that—a myth. It’s easy to get lost in a sea of overpriced options that promise perfection, but not all high-priced pads live up to the hype. In fact, many budget-friendly alternatives are engineered with advanced materials and thoughtful designs that ensure your polishing job is just as smooth, shiny, and flawless as it would be with pricier products.
What makes these affordable pads stand out is the thoughtful engineering behind them. They are crafted using premium foam and microfiber materials that are both durable and effective. These pads are designed to work efficiently with different types of polishes, whether you’re removing swirl marks or giving your car a glossy finish. One of the key features of low-cost pads is their versatility—many are suited for a wide range of surfaces, from automotive finishes to furniture or even floors. No matter what your polishing project is, these pads are up to the task.
The affordability of these polishing pads doesn’t mean they lack important features like proper ventilation, pressure distribution, or optimal cutting power. Good-quality pads have well-designed patterns that ensure an even application of polish and prevent the pad from getting clogged or unevenly worn. The even application minimizes the risk of leaving behind swirl marks or uneven buffing that could ruin the polished surface. For many, this means the cost savings don’t come at the expense of a professional-looking finish.
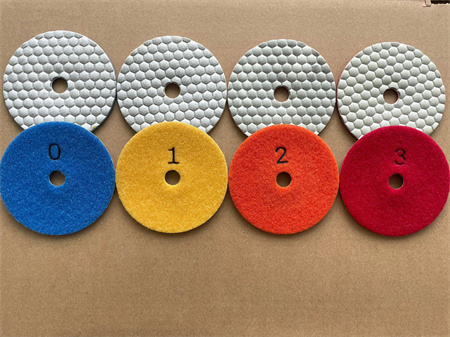
Durability is another key advantage of these low-cost pads. Unlike some cheaper options that break down quickly or lose their shape after just a few uses, quality budget pads are made to last. They’re built with robust materials that can withstand the pressures of multiple polishing sessions without wearing out too quickly. Whether you’re doing a single project or tackling a large, ongoing task, these pads hold up to the challenge without needing constant replacement.
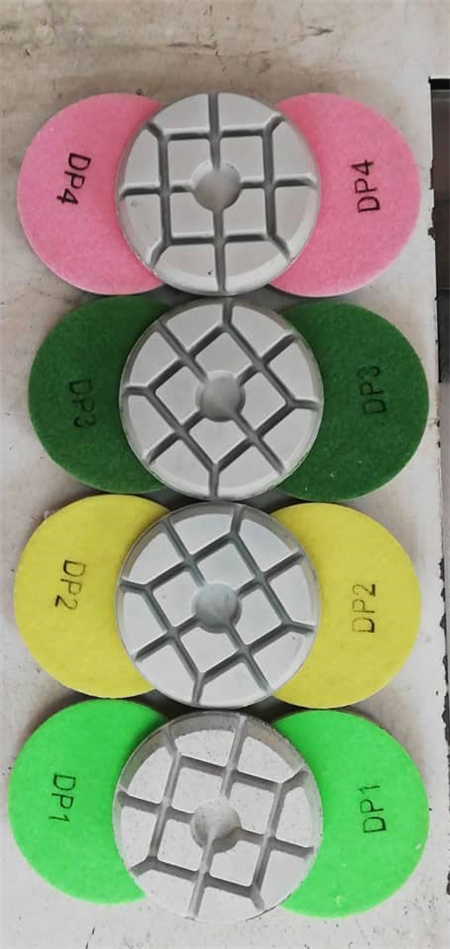
A major concern for anyone on a budget is getting value for money. The good news is that low-cost polishing pads that don’t sacrifice quality often provide exceptional value. They allow you to achieve the same high-quality results as the more expensive options but at a much more accessible price point. Whether you’re polishing a car, a piece of furniture, or tackling any other project that requires that perfect shine, you don’t need to spend an arm and a leg to get the job done right.
In the end, it’s clear that the cost of polishing pads doesn’t necessarily correlate with their performance. With a little research and a focus on quality materials and design, you can find low-cost options that do the job just as well as high-end pads. So, before you drop your cash on expensive pads, consider exploring the budget-friendly alternatives that deliver top-tier results without the hefty price tag.
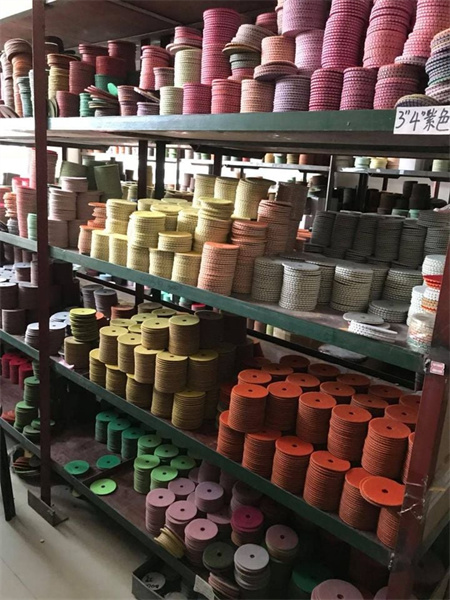