Polishing Slate Floors with Diamond Tools
Slate floors are a beautiful addition to any home or commercial space, offering durability, natural beauty, and a rustic charm that can’t be matched by many other flooring options. However, over time, the wear and tear from foot traffic, dirt, and spills can dull the surface of these stunning stones. This is where diamond tools come into play. Polishing slate floors with diamond tools is a powerful and effective way to restore their original luster and smooth out any imperfections.
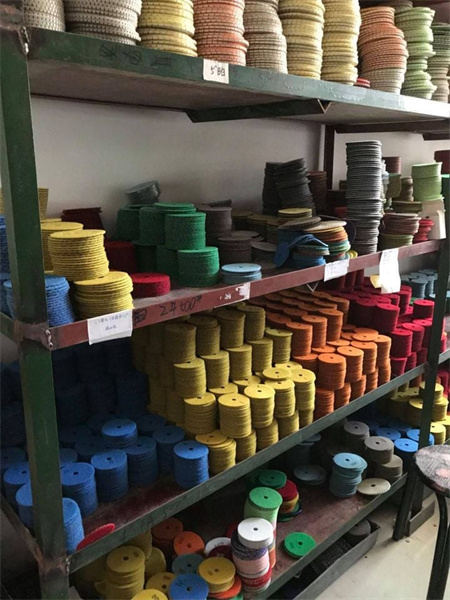
Diamond tools are the gold standard when it comes to polishing hard surfaces like slate. These tools are designed to grind and polish with incredible precision, harnessing the strength and hardness of diamonds to effectively smooth out surfaces without causing damage. They can be used to remove stains, scratches, and uneven areas, resulting in a floor that looks almost as good as new. What makes diamond tools particularly appealing is their ability to deliver a high-quality finish with minimal effort and time.
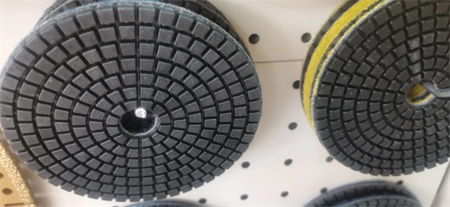
Once the surface is clean, the first stage of polishing typically involves using a coarser diamond pad to grind away the rough surface and address imperfections. This initial grinding helps to level the floor, smoothing out any major rough patches and removing surface stains. It’s important to take your time at this stage to avoid any deep gouges or uneven patches. After the initial grind, a finer grit diamond pad is used to refine the surface and begin the polishing process.
As the finer diamond pads are used, the surface becomes smoother, and the slate’s natural color and texture start to shine through. The process is slow and meticulous, but the results are undeniably worth the effort. Diamond polishing pads come in a variety of grits, with higher grits providing a more polished and glossy finish. This step not only enhances the aesthetics of the floor but also helps to create a more durable surface. Polishing with diamond tools strengthens the slate and makes it less likely to absorb dirt and stains, which can help maintain its appearance for a longer period.
A key benefit of polishing slate floors with diamond tools is the versatility they offer. Depending on the type of finish you’re aiming for, you can choose to create a high-gloss shine or a more matte, natural appearance. The flexibility of diamond tools allows you to cater to the specific look that suits your style and space. Plus, because the process is highly controlled, you can ensure that your slate retains its natural characteristics without being overly altered by the polishing process.
Another advantage is that diamond tools are efficient, saving time and effort compared to traditional polishing methods. While other types of abrasives can wear down quickly and may need to be replaced frequently, diamond tools are incredibly durable and can handle large areas with ease. This means fewer replacements and less downtime, which is a major perk for commercial applications or when dealing with large floor areas in homes.
After the polishing is complete, it’s essential to apply a sealing product to protect the slate. Sealing not only helps to maintain the polished look but also adds an extra layer of protection against dirt, stains, and moisture. The combination of diamond polishing and sealing can significantly extend the life of your slate floor, keeping it looking beautiful for years to come.
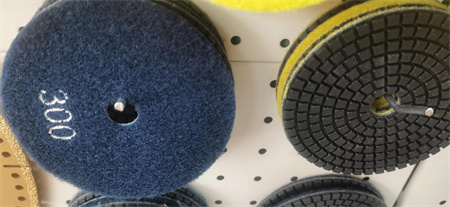