Why Seasonal Conditions Matter in Stone Restoration
Stone, with its timeless elegance, has been a cornerstone of architecture for centuries. Whether in historic buildings, sculptures, or monuments, stone has the ability to endure through ages, but like all materials, it’s not impervious to the elements. Over time, weather conditions take their toll, and when it comes to stone restoration, the role of seasonal conditions cannot be overlooked. The varying temperatures, humidity levels, and precipitation throughout the year can significantly impact the process and effectiveness of stone restoration, making it essential to consider these factors when planning any project.
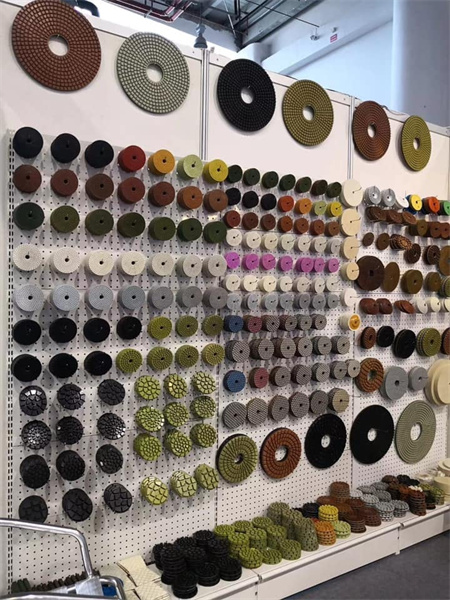
Spring and fall, with their moderate temperatures and lower humidity levels, are often the most ideal times for stone restoration. The moderate climate reduces the risk of thermal expansion or contraction, which can alter the stone’s structure. Additionally, the stable weather during these seasons allows for the use of more advanced restoration techniques, such as cleaning, repointing, or applying protective coatings. In spring, the end of frost and moisture buildup from winter allows stone surfaces to dry out adequately before any restoration work begins, while the fall provides an opportunity for finishing touches before the cold weather sets in again.
Humidity is another crucial factor that must be considered when restoring stone. High humidity levels can introduce excessive moisture into the stone, particularly porous types like limestone or sandstone. This not only makes cleaning and treatment more difficult but can also lead to the growth of mold or algae, which further deteriorates the stone’s integrity. Restoration specialists often adjust their techniques according to humidity levels, using low-moisture methods when possible to avoid trapping water inside the stone. The ideal conditions are those with a balance of moderate humidity and temperature, ensuring that any water used in the restoration process evaporates quickly and doesn’t linger in the stone, potentially causing damage.
Summers can be both a blessing and a curse for stone restoration. On the one hand, long hours of sunlight and dry weather can accelerate drying times for cleaned or treated surfaces, allowing for faster project completion. On the other hand, intense heat can cause stone to expand and crack, especially if the stone is exposed to direct sunlight for prolonged periods. It is critical for restoration professionals to avoid working during the hottest parts of the day and to ensure that stone surfaces are kept shaded or cool while restoration work is being carried out. Properly timed breaks and cooling methods can help mitigate the risks posed by high temperatures.
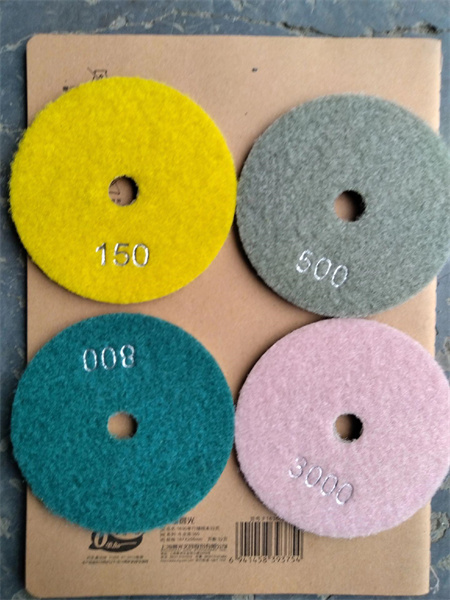
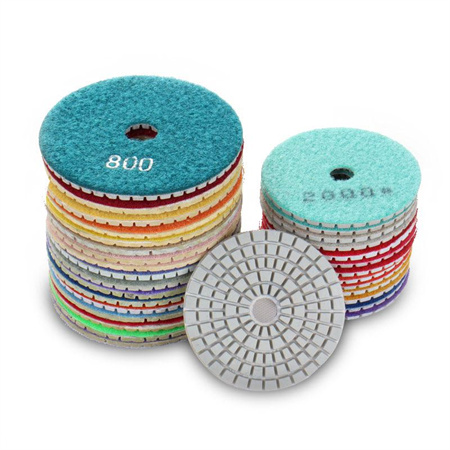
In conclusion, when embarking on a stone restoration project, paying close attention to seasonal conditions is crucial. Temperature fluctuations, humidity, and environmental factors can all have a profound impact on the success and longevity of restoration work. By carefully planning and selecting the optimal time for repairs, you ensure that the stone can withstand the test of time, not just in terms of age, but in quality of preservation. Whether you are preserving a historic building or simply maintaining the beauty of your stone surfaces, understanding how seasonal conditions affect the materials is key to achieving lasting results.