How to Order Customized Diamond Pads from Us
When it comes to finding the perfect diamond pads for your specific needs, customization is key. Whether you’re working in the automotive, construction, or polishing industries, having the right tools can make all the difference in efficiency and finish quality. If you’re looking for diamond pads that are tailored to your unique requirements, you’re in the right place. Here’s how to place an order with us and get exactly what you need.
Our team has years of experience working with a wide range of customers, and we understand that no two projects are the same. This is why we offer customized diamond pads that cater to your specific demands. From size and shape to grit and bonding material, we work closely with each client to ensure that every detail of the pad matches their precise needs.
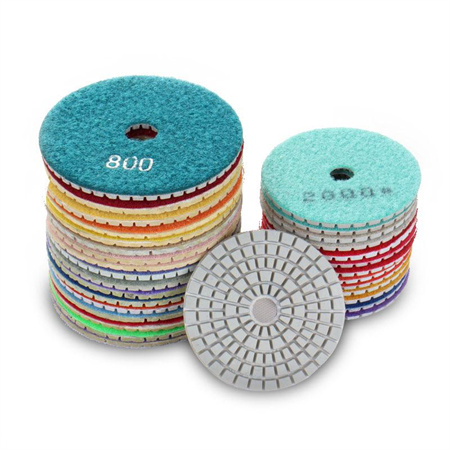
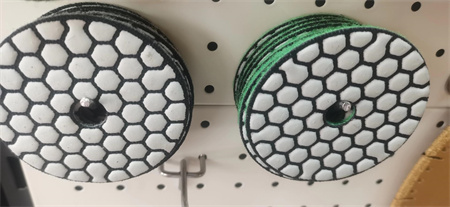
The next step is choosing the right specifications for your custom pads. The first thing to consider is the size and shape of the diamond pads. Whether you need them to be circular, square, or any other form, we can manufacture pads that fit your equipment or machinery perfectly. We also offer pads in a range of diameters and thicknesses, depending on the depth of the surface material you’re working with and the kind of pressure your project requires.
Grit selection is another crucial element. Diamond pads are available in various grits, ranging from very coarse to ultra-fine. If you’re preparing a surface for heavy-duty grinding or smoothing it out with a fine finish, selecting the right grit is essential. Our experts will walk you through your options, ensuring you choose the grit that delivers the best results for your project. Custom grits are also available if you have very specific polishing or cutting needs.
We understand that the bond strength of the diamonds to the pad itself is a critical factor in its durability and performance. Depending on whether your work involves dry or wet conditions, we’ll help you choose the right bonding material. From metal-bonded pads to resin-bonded ones, we offer a variety of options that are designed to withstand your unique working conditions. Resin bonds, for instance, are perfect for finer finishes and can withstand high-pressure polishing, while metal bonds are ideal for more aggressive grinding.
Once all the details have been finalized, we’ll move on to production. Our team uses advanced manufacturing techniques to ensure your customized diamond pads meet the highest standards. We take pride in delivering products that not only perform well but also stand the test of time, even under tough working conditions.
Upon completion of the production, we’ll send your custom diamond pads to you in a timely manner. We offer flexible shipping options to ensure you receive your order as quickly as possible, and our dedicated customer service team will provide tracking details so you can keep an eye on the status of your shipment.
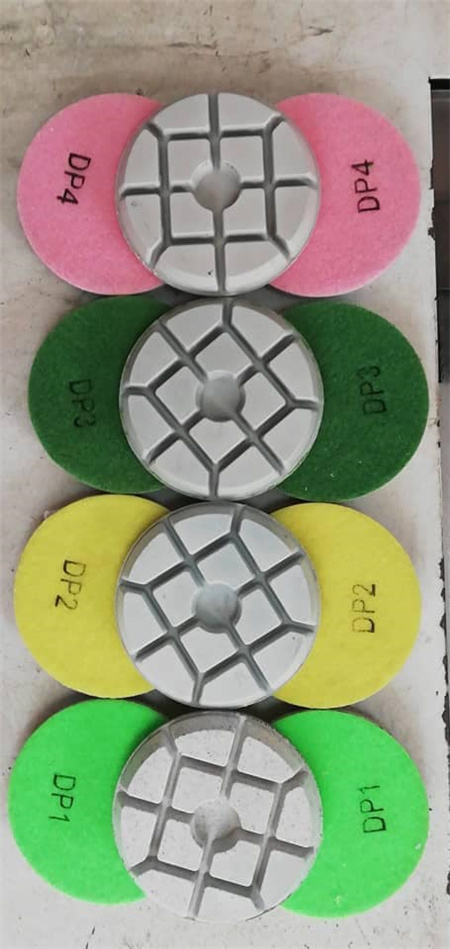
Ordering customized diamond pads from us is a straightforward and reliable process. With our expertise and commitment to quality, you can rest assured that you’re getting the best tools for your specific needs. So, if you’re ready to take the next step in enhancing your operations, get in touch with us today and let’s start crafting the perfect diamond pads for you.