Trends in Polishing Pads for Residential and Commercial Applications
Polishing pads are essential tools in both residential and commercial settings, used to bring out the best in a variety of surfaces. Whether it’s restoring the shine of marble floors in a home or maintaining the cleanliness and smoothness of concrete floors in a commercial space, the role of polishing pads cannot be overstated. Over the years, these pads have evolved, and several key trends are shaping the future of polishing technology.
One of the most notable trends is the shift towards eco-friendly and sustainable polishing pads. As industries across the world move toward greener solutions, polishing pad manufacturers are responding with materials that reduce environmental impact. Traditional polishing pads, often made from synthetic materials or harsh chemicals, are being replaced by more sustainable options, such as those made from biodegradable fibers or recycled materials. These pads not only help reduce waste but also offer comparable performance to their synthetic counterparts, making them a popular choice for both residential and commercial applications.
In addition to environmental considerations, the demand for advanced technology in polishing pads is on the rise. In particular, advancements in pad composition and design have made it easier for users to achieve a superior finish with less effort. Modern polishing pads incorporate advanced abrasives, like diamond crystals or ceramic particles, which allow for more efficient material removal and a smoother, glossier finish. These innovations have made it possible to polish a wider range of surfaces, including delicate marble and granite, with greater ease and precision.
Another trend that is gaining momentum is the development of multi-functional polishing pads. In the past, different pads were needed for various stages of polishing—coarse pads for initial grinding, medium pads for refinement, and fine pads for finishing. Today, manufacturers are creating pads that combine multiple functions into one product, allowing users to achieve high-quality results without needing to switch between pads. This innovation not only saves time but also reduces the complexity of the polishing process, making it easier for professionals and DIYers alike to achieve professional-grade results.
Durability and longevity are also becoming key considerations in the design of polishing pads. In commercial settings, where pads are subjected to intense and continuous use, it’s essential that they maintain their performance over time. New materials and construction techniques are being used to produce pads that are more durable, resistant to wear, and able to withstand prolonged exposure to heat and pressure. This trend ensures that polishing pads in commercial environments, such as hotels, hospitals, and retail spaces, provide consistent results without needing frequent replacements.
For residential applications, the trend is toward more user-friendly and versatile pads. Homeowners are looking for solutions that can easily handle a variety of surfaces, from hardwood floors to tiles to natural stone. Polishing pads designed for home use are often lighter, simpler to operate, and come in user-friendly formats that fit a range of cleaning machines. Some pads are even designed to be compatible with home-grade floor polishers, making it easier for non-professionals to achieve professional-level results.
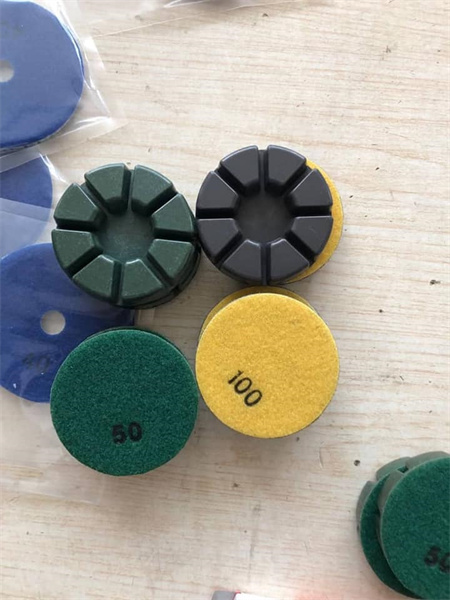
Lastly, the customization of polishing pads for specific applications is becoming more common. Manufacturers are now designing pads tailored to particular types of flooring materials, ensuring that each surface receives the most appropriate care. Whether it’s a pad specifically designed for polishing hardwood floors or one that excels on terrazzo, customization allows for more targeted, efficient cleaning and polishing.
As the polishing pad industry continues to evolve, these trends reflect the growing demand for efficiency, sustainability, and user-centered design. Whether used in residential or commercial settings, polishing pads are becoming more sophisticated and accessible, providing users with the tools they need to keep surfaces looking pristine with minimal effort. With advancements in technology and materials, the future of polishing pads is brighter than ever, and it’s clear that innovation will continue to drive the development of this essential tool.
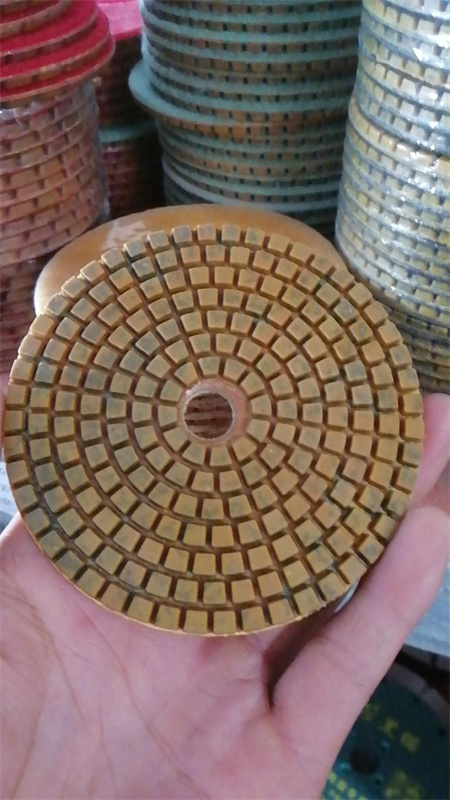
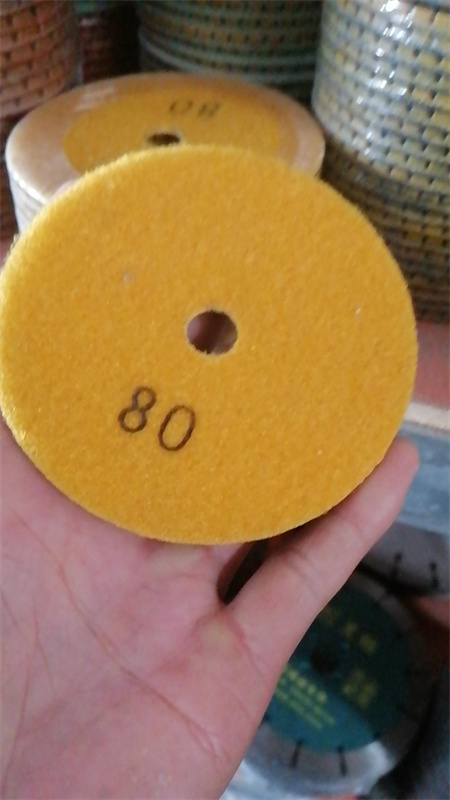