Polishing terrazzo floors with diamond pads is an effective and efficient way to restore their shine and bring out the natural beauty of the surface. Over time, terrazzo can become dull and scratched due to foot traffic, dirt, and general wear. But with the right tools and technique, you can revive it to its original luster, making it a stunning focal point in any space. Here’s a guide to help you master the art of polishing terrazzo floors using diamond pads.
First, understanding terrazzo is essential. Terrazzo is a composite material made of chips of marble, granite, quartz, or glass, all embedded in a cement or epoxy base. Its appeal lies in its durability and unique, customizable design. But while it is tough, it does require some care to maintain its glossy finish. Polishing terrazzo with diamond pads is one of the best ways to restore its shine and ensure its longevity.
Diamond pads are the go-to tool for polishing terrazzo floors. These pads are made with industrial-grade diamonds embedded into a resin bond, offering superior cutting power and a long lifespan. They come in various grits, from coarse to fine, allowing you to tailor the polishing process to the condition of your floor. Choosing the right grit is crucial to achieving the perfect finish.
Before you begin polishing, ensure the floor is clean and free from dust, dirt, and debris. Sweeping or vacuuming the floor thoroughly will prevent any particles from scratching the surface during the polishing process. Once cleaned, dampen the terrazzo surface slightly with water, as working with a wet surface helps the pads glide smoothly and prevents excessive heat buildup. The water also helps keep the floor from becoming too dusty.
Now, it’s time to start with the lowest grit diamond pad. If your terrazzo floor has visible scratches or has not been polished in a long time, starting with a coarser grit will help remove imperfections and smooth out the surface. Work the pad in a circular motion, applying light pressure. Don’t rush this step—allow the pad to work its way through the floor, gradually smoothing out the imperfections. The goal is not to grind down the terrazzo but to remove the top layer of damage.
Once the floor looks smooth and free of visible damage, you can move to a finer grit pad. Each grit level refines the surface further, removing the marks left by the coarser pads. This step is where the terrazzo starts to show its true beauty, as the polishing process reveals the full brilliance of the marble or glass chips embedded in the floor. With each finer grit, you will notice the floor becoming more lustrous and reflective.
As you move through the different grits, it’s important to keep the floor wet. Not only does water reduce friction and prevent heat buildup, but it also ensures that the pads stay effective longer by washing away debris that might get trapped between the pad and the floor. After completing each grit stage, wipe the floor to remove any remaining slurry and dirt before moving on to the next grit.
Polishing terrazzo floors with diamond pads requires patience and attention to detail. The process can take some time, but the results are worth it. If done correctly, your floor will have a smooth, glossy finish that will enhance the overall look of your space. The surface will also be more durable, as the diamond pads help to seal and strengthen the terrazzo, providing long-lasting protection against future damage.
One key aspect to keep in mind is the use of a floor buffer. A floor buffer or grinder is often necessary when working with large terrazzo areas, as it allows for more even pressure and consistent results. If you’re working on a small area, a handheld machine or even a polishing attachment for a regular floor cleaner might suffice. However, for larger spaces, it’s worth investing in the right equipment to ensure a professional-quality finish.
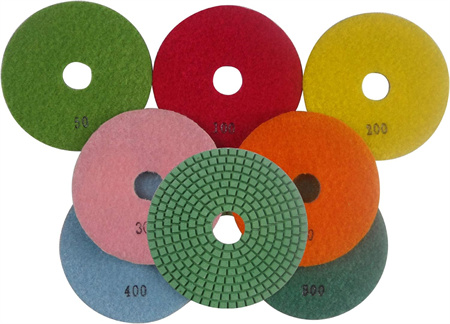
Regular maintenance is also important. While diamond polishing can restore the floor’s appearance, routine cleaning and care will help keep it looking its best. Sweeping and mopping the floor regularly with a mild, non-abrasive cleaner will help preserve the shine achieved from polishing.
In conclusion, polishing terrazzo floors with diamond pads is a straightforward process that requires the right tools, some patience, and a keen eye for detail. By following these tips, you can bring your terrazzo floors back to life, enhancing their natural beauty and extending their lifespan. Whether you’re preparing a space for guests, giving your home a fresh update, or maintaining a commercial property, polished terrazzo is a timeless choice that will continue to impress for years to come.
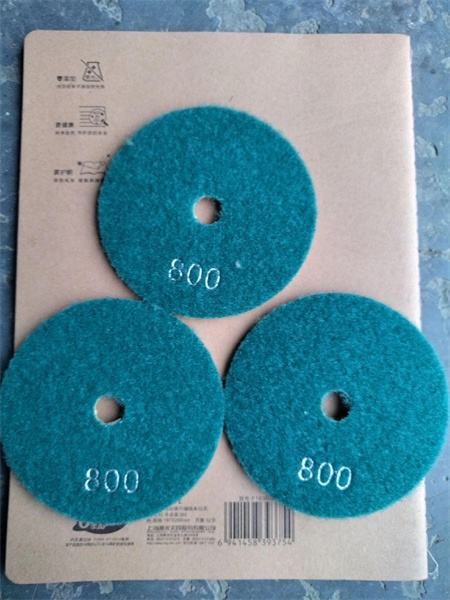