Bulk Buying Tips for International Importers
When it comes to international trade, bulk buying is one of the most effective strategies for importers looking to maximize profits while minimizing costs. Bulk purchases can provide significant savings, streamline logistics, and help build strong supplier relationships. However, this approach comes with its own set of challenges that can impact your bottom line if not managed properly. To help you navigate the complexities of bulk buying, here are some practical tips that can make a real difference.
Understanding Market Trends and Product Demand
One of the most crucial steps before diving into bulk purchases is understanding the market trends and the demand for the products you intend to import. Knowing whether a product is in season, its anticipated future demand, or potential changes in consumer preferences can significantly influence your buying decisions. If you’re importing goods that have a short shelf life or are subject to seasonal fluctuations, bulk buying could backfire if the product doesn’t sell as expected.
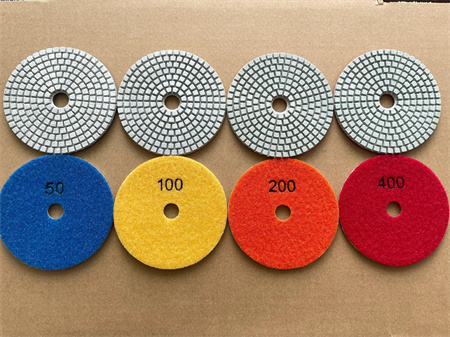
Evaluating Supplier Reliability
When buying in bulk, you’re not just looking for the lowest price – supplier reliability is equally important. A reliable supplier can ensure consistent product quality, timely delivery, and good communication. If your supplier fails to deliver or sends subpar products, your entire business could be at risk, especially when you’re dealing with large quantities.
Before committing to bulk orders, take the time to evaluate potential suppliers carefully. Look for businesses with a proven track record of quality and reliability. Request samples and references, and check reviews from other importers. A strong, trustworthy supplier will be transparent about their production processes and logistics capabilities, which can save you from headaches down the line.
Negotiate the Best Terms
Negotiation is key when you’re buying products in bulk, especially if you’re an international importer dealing with suppliers across borders. Bulk orders often provide leverage for negotiating better pricing, favorable payment terms, and discounts. Suppliers are more likely to offer attractive pricing structures or even additional benefits when they know they’re dealing with a larger order.
When negotiating, always factor in all associated costs—shipping, customs, taxes, and any additional charges. Sometimes, the upfront price may seem like a great deal, but hidden fees can turn what seemed like a bargain into a costly mistake. By having clear communication with your supplier about these costs, you can ensure that your bulk buying strategy remains financially viable.
Managing Shipping and Logistics
Shipping and logistics are often the most complex aspects of bulk buying for international importers. With larger quantities of goods, coordinating the shipment can involve navigating international shipping routes, understanding customs regulations, and dealing with potential delays. To avoid unnecessary costs and disruptions, it’s crucial to have a reliable logistics partner who understands the intricacies of international shipping.

Storing and Managing Inventory
After securing your bulk purchase, proper inventory management becomes essential. It’s one thing to have a warehouse full of products, but it’s another to manage them effectively. Storing large quantities of goods requires careful planning, especially when dealing with perishable or sensitive items. Invest in a reliable inventory management system that can help you track stock levels, monitor product conditions, and ensure that your goods are readily available when needed.
Moreover, think about warehousing options and their associated costs. If you’re importing large volumes of goods, it might make sense to negotiate long-term storage agreements or even establish warehouses closer to your key markets, reducing both shipping times and costs in the long term.
Understanding Customs and Import Regulations
Navigating the labyrinth of customs regulations is a common pain point for international importers. Bulk buying can sometimes mean dealing with higher scrutiny from customs officials, particularly if you’re importing large quantities of goods. Understanding import duties, taxes, and the documentation required for clearance can save you both time and money.
Ensure you’re familiar with the customs requirements for both your home country and the country you’re importing from. Working with a customs broker or a trade consultant can be incredibly helpful if you’re unfamiliar with the process. They can guide you through the complexities of paperwork, help you avoid costly mistakes, and ensure that all legal obligations are met.
Mitigating Risk
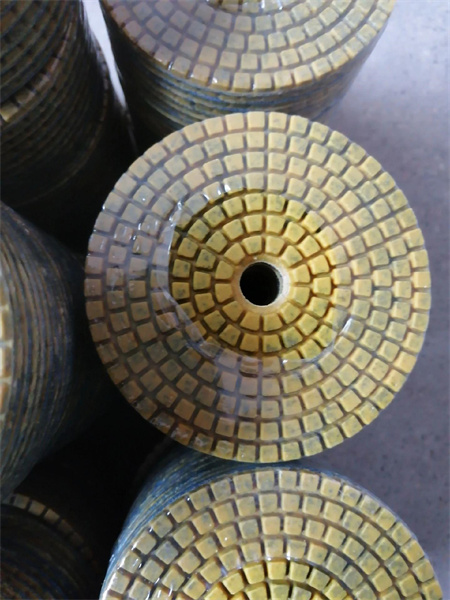
Additionally, consider using insurance to cover potential losses during shipping or if goods are damaged upon arrival. While it might seem like an added expense, the peace of mind it provides can be invaluable, especially when dealing with large orders.
Bulk buying can be a game-changer for international importers, but it’s essential to approach it with careful planning and consideration. By understanding the market, choosing reliable suppliers, negotiating the best terms, and ensuring smooth logistics, you can make the most of bulk purchasing. Keep your risk management strategy in mind and ensure that your inventory is efficiently managed. With the right approach, bulk buying can offer substantial benefits and boost your business’s profitability in the competitive world of international trade.