Balancing Speed and Efficiency in Diamond Pad Polishing
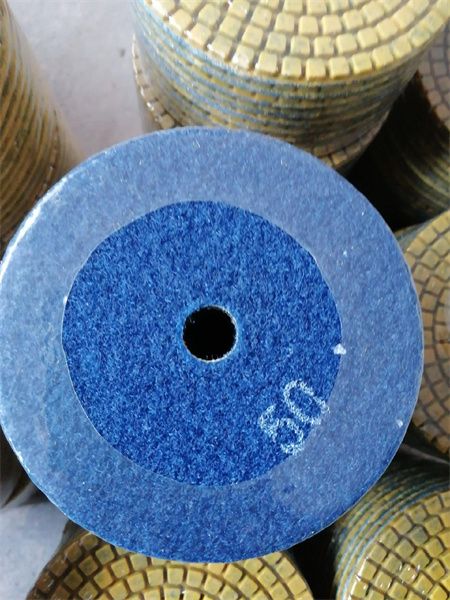
When it comes to diamond pad polishing, speed is often the first consideration. Faster processes typically lead to higher productivity, which is essential in high-demand sectors. But it’s important to remember that pushing the polishing process too aggressively can lead to reduced quality, compromised surface integrity, and a higher rate of defect. In this delicate balancing act, the goal is not simply to go faster but to find the sweet spot where both speed and quality meet without one detracting from the other.
Understanding the dynamics of diamond pad polishing begins with recognizing the different variables that impact the polishing process. The type of diamond pad, the material being polished, the equipment used, and the settings all play crucial roles. Choosing the right diamond pad is vital—pads come in different grades, and each is designed for specific types of surfaces. A high-quality pad that matches the material can optimize the process, reducing the need for excessive time spent polishing.
The speed of the process is largely influenced by the pressure applied and the rate of movement across the surface. Higher speeds can remove material more quickly, but if the pressure is too high or the speed too fast, the risk of over-polishing or damaging the material increases. A methodical, controlled approach allows the technician to gradually refine the surface while preventing excessive wear. Thus, the importance of fine-tuning the pressure and speed of the machine cannot be overstated.
Another factor that contributes to both speed and efficiency is the use of advanced polishing equipment. High-end machines allow for precise adjustments to pressure, speed, and even the angle of the polishing pad. With automation and computerized control systems becoming more common, it’s easier to maintain consistent pressure and speed throughout the process. These machines can also offer real-time feedback, which helps technicians make on-the-fly adjustments to maintain optimal results.
Efficiency in diamond pad polishing is also linked to the process’s ability to remove contaminants and produce a uniform surface finish. Speed alone does not guarantee efficiency—if polishing pads wear out too quickly or the process causes excessive material loss, it can end up being counterproductive. By using high-quality diamond abrasives that are both durable and effective, companies can ensure that the polishing process not only runs quickly but also minimizes waste and wear on equipment.
But perhaps the most significant challenge in balancing speed and efficiency is operator skill. While the technology behind polishing machines has advanced, the expertise of the technician remains crucial. A skilled operator knows how to read the material, adjust the machine settings, and make judgment calls when it’s necessary to slow down to ensure the finish is flawless. This human factor remains indispensable, particularly in industries where precision is paramount.
Training and experience contribute to optimizing both speed and efficiency in polishing. As operators gain more insight into the materials they’re working with and become familiar with the specific characteristics of their polishing pads, they can adjust the process dynamically to achieve the best results. Experience also helps in troubleshooting and resolving potential issues before they escalate into costly delays.
In recent years, technological advancements have also led to the development of new types of diamond pads that provide faster polishing with less material loss. These pads feature specialized coatings or diamond particles that improve the efficiency of the polishing process, allowing for better results in less time. Such innovations play a significant role in meeting the demands for both speed and quality, offering manufacturers a solution that doesn’t compromise one for the other.
Ultimately, balancing speed and efficiency in diamond pad polishing is an ongoing process of fine-tuning. It requires the right combination of quality materials, sophisticated equipment, skilled operators, and continual process improvements. As industries push for faster turnaround times and higher production rates, finding this balance is essential for ensuring that the finished product meets the highest standards without sacrificing precision or quality.
In conclusion, diamond pad polishing is not just about getting the job done faster; it’s about achieving the perfect harmony between speed and efficiency. By investing in the right tools, leveraging technological advancements, and continually honing the skills of operators, manufacturers can optimize their polishing processes to produce flawless results at a pace that meets market demands.
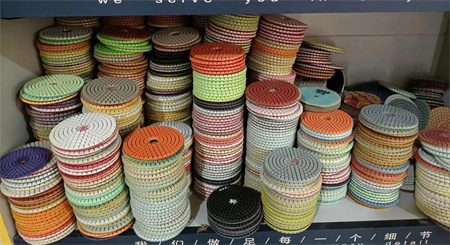
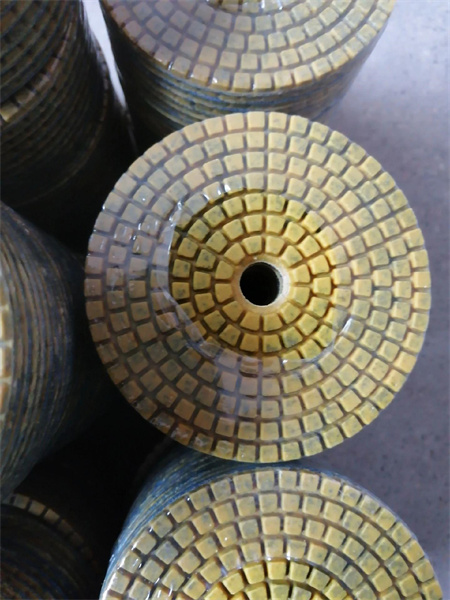