Future of Diamond Polishing Pads in the Construction Industry
The construction industry has always been a field of innovation, with new technologies and materials constantly reshaping the way projects are executed. One such innovation that has quietly revolutionized the way surfaces are finished is the diamond polishing pad. As construction projects grow more complex and demand higher standards of quality, these pads are quickly becoming an indispensable tool for professionals who aim for perfection in their work. Looking ahead, the role of diamond polishing pads in construction seems poised for an exciting future.
Over the past few years, diamond polishing pads have evolved significantly. Initially designed for marble and granite, they have become essential for polishing a wide range of materials, from concrete to terrazzo and even newer synthetic surfaces. Their ability to achieve an ultra-smooth finish, combined with their durability, makes them a preferred choice for construction workers and contractors around the world. However, it’s not just their versatility that makes them stand out in the industry—it’s the continuous advancements in their design and performance that are setting the stage for their future.
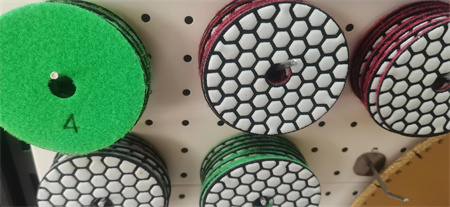
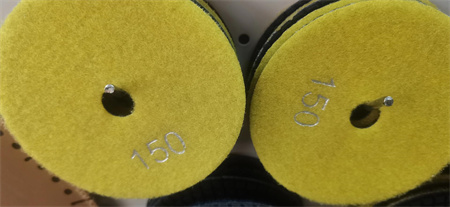
The advent of robotic technology and automated machinery in the construction sector also bodes well for the future of diamond polishing pads. Automated systems are increasingly used for tasks like floor grinding and surface polishing, and diamond polishing pads are an integral part of these systems. Robots equipped with diamond pads can polish large areas quickly and precisely, reducing the need for manual labor while ensuring consistent results. This shift towards automation will drive demand for high-performance diamond polishing pads, which can withstand the rigorous demands of robotic operations without losing effectiveness.
Efficiency and speed are at the heart of every construction project, and diamond polishing pads are becoming more efficient with each generation. Innovations in the materials used to manufacture these pads, including improved diamond bonding technology, are enabling them to maintain cutting power over a longer lifespan. As a result, construction workers can complete polishing jobs faster, with less downtime for equipment maintenance. This efficiency not only translates to cost savings but also increases productivity on job sites, allowing contractors to meet tight deadlines without compromising on quality.
Additionally, diamond polishing pads are becoming more affordable due to advancements in manufacturing processes. As demand for these pads increases and production techniques improve, costs have been steadily decreasing, making them accessible to a broader range of construction professionals. This accessibility will continue to drive their adoption, allowing smaller contractors to leverage the advantages of diamond polishing pads without breaking their budgets.
Looking further ahead, the integration of digital technology could also play a role in the future of diamond polishing pads. Imagine a world where polishing pads are embedded with sensors that monitor the pad’s wear and provide real-time data on surface conditions, performance, and optimal usage. This could revolutionize the way construction professionals approach polishing, allowing them to make data-driven decisions about when to replace pads, adjust their techniques, and optimize their workflow for maximum efficiency.
The future of diamond polishing pads in the construction industry looks bright. As technology continues to evolve, these tools will only get better—more durable, more efficient, and better suited for the diverse range of materials and surfaces found on today’s job sites. Whether it’s reducing environmental impact, improving safety, or streamlining operations, diamond polishing pads are set to play an even more critical role in shaping the construction industry’s future. For contractors and construction professionals, embracing these innovations will be key to staying competitive and ensuring top-quality finishes in every project.
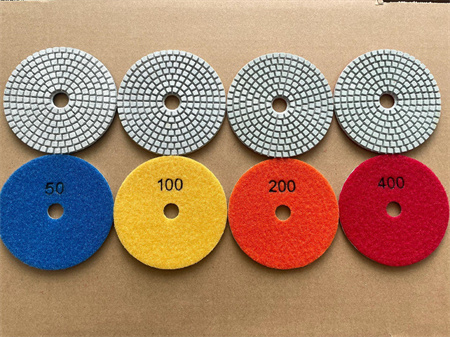