Diamond polishing pads are essential tools in the stone and concrete polishing industries, and producing them involves a meticulous process that combines precision, high-quality materials, and expert craftsmanship. The journey of creating these pads starts with selecting the finest diamond particles. These diamonds are chosen for their hardness and ability to achieve a smooth, high-gloss finish on various surfaces.
The diamond particles are blended with a bonding material to create a mixture that will form the body of the pad. The next step is the molding process, where the mixture is pressed into the desired shape and size, typically a circular disc. This is a critical stage, as the pressure applied during molding ensures that the diamonds are evenly distributed, which directly impacts the performance of the polishing pad.
Once the basic shape is formed, the curing process begins. The pad is placed in a specialized oven where heat is applied to harden the bonding material, which locks the diamonds in place. This step ensures that the pad is durable and can withstand the intense friction and heat generated during polishing.
After curing, the pads go through a process of quality control. Each pad is carefully inspected for any defects and tested for consistency in terms of diamond distribution, hardness, and durability. Pads that do not meet the stringent standards are discarded, ensuring that only the highest-quality products reach customers.
In the final stages, the pads are polished to smoothen their surfaces and improve their finishing capabilities. This fine-tuning is crucial as it allows the pad to work efficiently on stone, concrete, and other surfaces, providing a smooth and glossy result without causing damage.
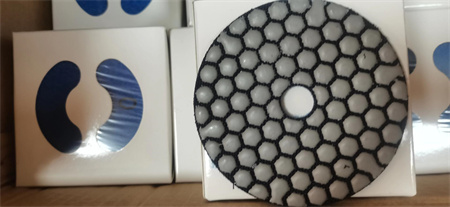
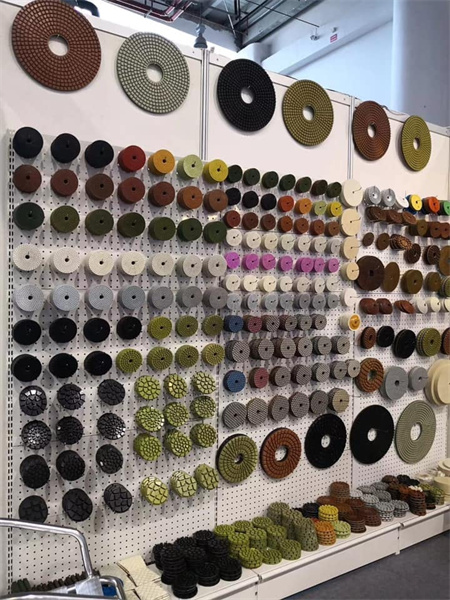
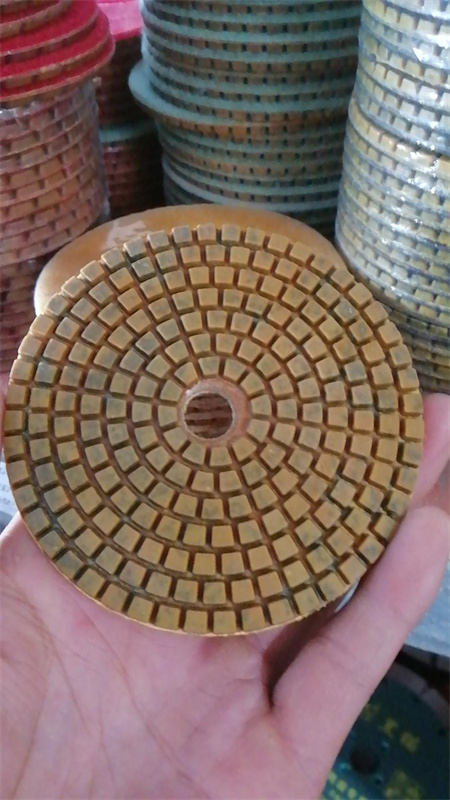