Achieving Seamless Polishing on Narrow Edges
When it comes to precision manufacturing or fine craftsmanship, the process of polishing narrow edges presents a unique set of challenges. Whether you’re working with metals, glass, plastics, or any other material, perfecting those slender borders is crucial for both aesthetic appeal and functional performance. But how exactly can one achieve that flawless, mirror-like finish on such delicate surfaces?
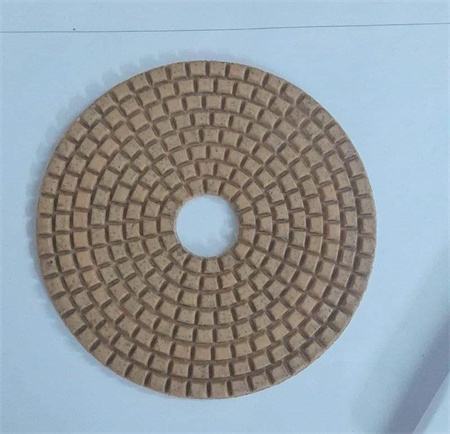
One of the first steps in mastering this task is selecting the proper abrasive materials. Unlike broader surfaces that may be polished using a range of coarser abrasives, narrow edges demand a more meticulous approach. Fine-grit abrasives, such as diamond-infused pads or ultra-fine polishing compounds, are ideal for these precision tasks. These materials allow for gradual removal of small amounts of material, which is essential when working with thin edges that can easily be damaged by overly aggressive polishing.
It’s not just about the abrasives, though. The technique plays an equally important role in achieving a seamless finish. A slow, controlled motion ensures that the polishing process is consistent and that the pressure is evenly distributed across the edge. Rushing the task or applying too much force can result in uneven polishing or even microfractures along the edge. Whether you’re polishing by hand or with a machine, maintaining steady, light pressure is key to avoiding these issues.
Polishing narrow edges often requires a different approach depending on the material being worked with. For metals, such as aluminum or stainless steel, a combination of abrasives and polishing compounds designed specifically for metal surfaces will yield the best results. For softer materials like plastic, using a fine abrasive combined with a non-abrasive, polishing solution ensures a smooth, glossy finish without compromising the material’s integrity.
Heat buildup is another challenge that can occur during the polishing process, especially when working with metals or harder materials. As friction between the polishing tool and the material increases, so does the heat, which can lead to discoloration or surface damage. Using a lubricating compound or water-based coolant can help dissipate heat and maintain a consistent temperature throughout the process. Additionally, working in shorter intervals and allowing the material to cool down between passes can prevent overheating and preserve the integrity of the edge.
Another critical aspect of achieving a seamless polish on narrow edges is the alignment and setup of your equipment. Whether you’re using a manual tool or an automated system, ensuring that the edge is properly aligned is vital to avoid inconsistencies in the polishing process. Any misalignment, even by a fraction of a degree, can result in uneven pressure distribution, leading to an imperfect finish. Ensuring that the material is securely held in place and that your polishing tool is properly calibrated will help maintain consistency across the entire edge.
Precision matters, not just in terms of the final finish, but also in controlling the depth of the polish. It’s essential to ensure that the polishing action is confined to the edges, leaving the main surface untouched. This can be challenging when dealing with small, narrow areas, where there is little room for error. In many cases, polishing narrow edges by hand or with specialized machinery equipped with fine tools ensures the depth of the polish remains controlled and consistent.
In some cases, achieving a seamless finish may require multiple stages of polishing. Starting with a coarse abrasive, gradually working through finer grits, and then finishing with a polishing compound can help refine the edge while removing any residual imperfections. Each step should be carried out with care, ensuring that no grit from the previous stage remains, which could create scratches or dullness.
The final result is more than just a polished surface—it’s a testimony to craftsmanship and precision. Whether it’s the sharp edge of a blade, the sleek corners of a smartphone, or the fine details on an aerospace component, achieving a perfect finish on narrow edges signifies not only quality but also attention to detail. This process demands patience, skill, and the right tools. But when done right, the result is nothing short of perfection—an edge that gleams with a seamless polish, enhancing both the aesthetic appeal and functionality of the product.
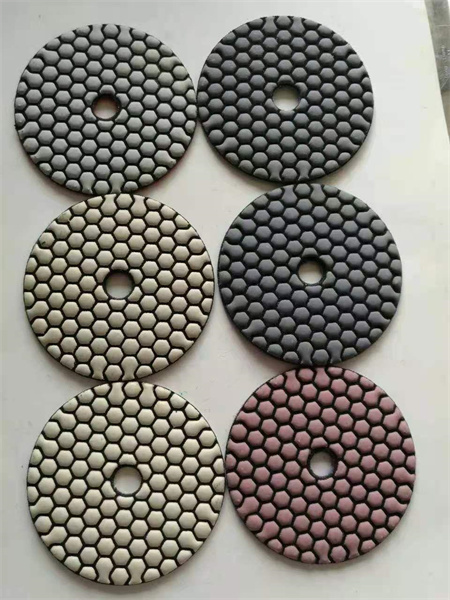
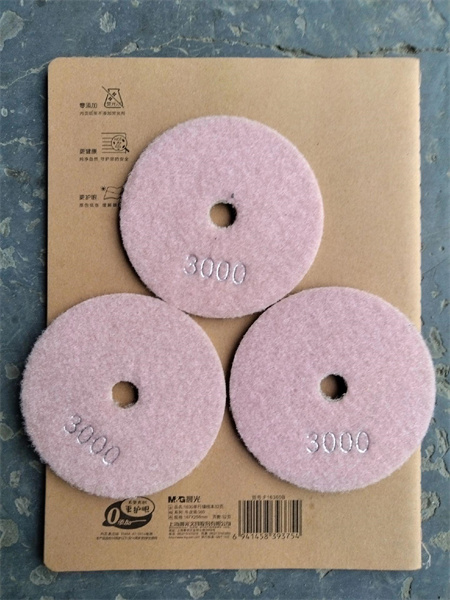