The Role of Automation in Diamond Tool Manufacturing
Diamond tools are among the most durable and efficient tools used in various industries, from cutting and grinding to polishing and drilling. Their unmatched hardness and precision make them indispensable in sectors such as aerospace, automotive, and electronics. However, the production of these intricate and high-performance tools has traditionally been a labor-intensive and time-consuming process. Enter automation: the game-changer that has revolutionized diamond tool manufacturing, enhancing efficiency, precision, and overall productivity.
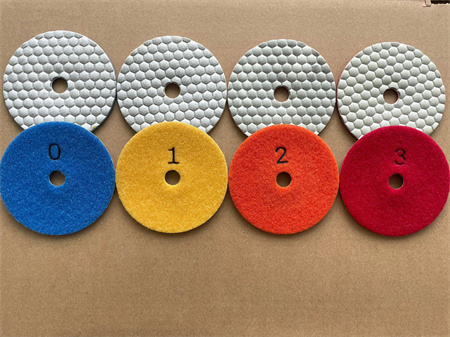
In diamond tool production, one of the most significant areas where automation plays a crucial role is in the shaping and grinding processes. Traditional methods required skilled workers to manually control machines, a task that not only took considerable time but also depended on human expertise. With the introduction of automated machinery, these processes have become faster and more consistent. CNC (Computer Numerical Control) machines are now widely used to shape and grind diamond tools with a level of accuracy that would be extremely difficult to achieve manually. The integration of robotics further streamlines these tasks by reducing human intervention, lowering the chances of variability, and improving the overall consistency of the finished product.
Beyond shaping and grinding, automation has also transformed the bonding process, where diamond particles are securely attached to the tool substrate. In the past, this step was susceptible to inconsistencies, as it required careful handling of materials under controlled conditions. Today, automated bonding systems ensure that the diamond particles are uniformly distributed and securely fixed in place, creating a stronger bond that improves the tool’s performance and lifespan. Moreover, automated systems can monitor temperature, pressure, and other variables in real-time, making adjustments as necessary to maintain optimal bonding conditions. This level of control not only enhances the quality of the tools but also contributes to more efficient use of resources.
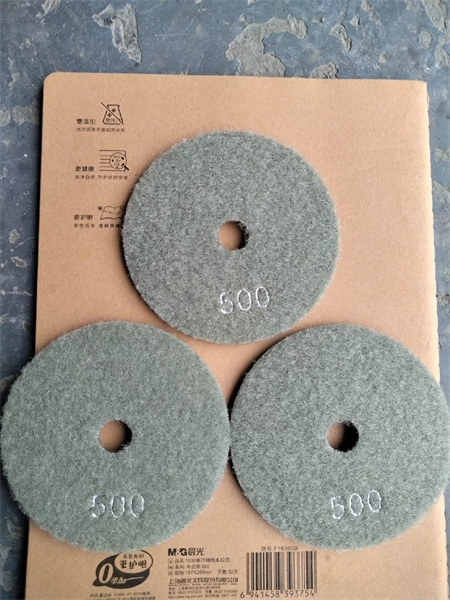
Automation also addresses one of the key challenges in diamond tool manufacturing: maintaining a consistent production rate. Since the production of high-quality diamond tools requires meticulous attention to detail, production cycles can be slow. Automated systems work tirelessly, 24/7, ensuring that production never slows down and that each tool is produced with the same high level of consistency. This continuous production capability is especially valuable in industries that require large volumes of diamond tools, such as the automotive and electronics sectors, where supply chain reliability is critical.
Moreover, automation in diamond tool manufacturing doesn’t just benefit the production process; it also has a positive impact on worker safety and ergonomics. Many tasks involved in the production of diamond tools are physically demanding and can be hazardous. By automating dangerous or repetitive processes, workers can focus on more complex tasks that require their expertise, ultimately leading to a safer work environment. In the long run, this not only improves employee well-being but also reduces the risk of costly workplace accidents.
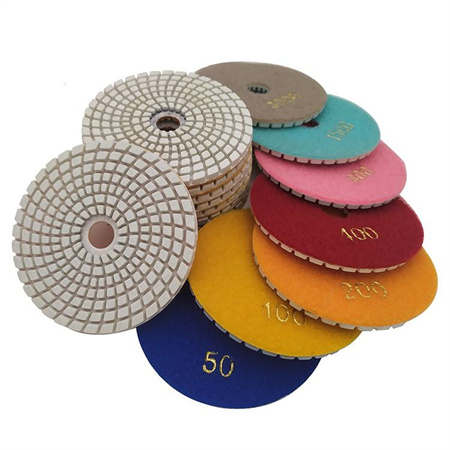
In conclusion, automation has become an indispensable part of diamond tool manufacturing, bringing significant improvements in speed, precision, and consistency. As technologies continue to evolve, we can expect automation to play an even greater role in advancing the capabilities of diamond tools and their production processes. By reducing errors, improving quality, and increasing efficiency, automation is helping manufacturers meet the ever-growing demand for high-performance diamond tools across a wide range of industries. The future of diamond tool manufacturing is undoubtedly automated, and the results speak for themselves—superior products, greater productivity, and a more sustainable manufacturing process.