Durability Testing of Diamond Polishing Pads
When it comes to achieving a flawless finish on surfaces like stone, glass, or concrete, diamond polishing pads are often the tool of choice. Known for their exceptional ability to smooth and refine tough materials, these pads have become indispensable in industries ranging from construction to automotive. However, their effectiveness isn’t just about the sharpness or quality of the diamond particles embedded in them. The real value lies in their durability. Understanding how well a diamond polishing pad holds up over time can drastically affect both the quality of the work and the costs involved. That’s where durability testing comes in—a critical process that ensures these pads can endure the rigorous demands of polishing without losing their performance.
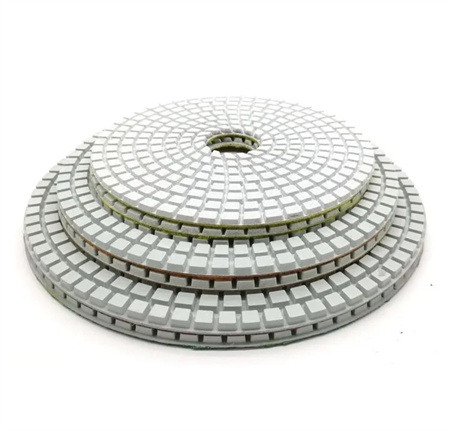
To start, testing typically involves a series of controlled polishing cycles, where the pads are put through rigorous abrasion. The most straightforward method is to run the pad against a rough surface under a set pressure, measuring how much material is removed over time. The test continues until a noticeable degradation in performance occurs—whether that’s a decrease in polishing ability, the loss of diamond particles, or the overall breakdown of the pad’s structure. Observing how long the pad maintains its efficiency in these challenging conditions gives manufacturers, as well as end-users, a reliable sense of its potential lifespan.
A critical factor in these tests is the evaluation of how the pad responds to heat. Polishing generates friction, which leads to temperature spikes, especially when working on dense materials like granite or concrete. Too much heat can cause the bond between the diamonds and the pad to weaken, which can quickly reduce its effectiveness. Durability tests that monitor heat resistance are invaluable for understanding whether the pad can maintain its integrity and continue to perform optimally despite these intense conditions.
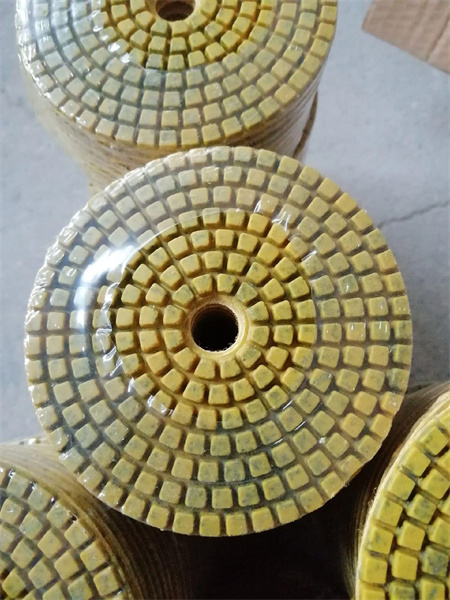
One of the most significant factors in the overall durability of diamond polishing pads is the quality of the diamonds used in the manufacturing process. Diamonds are graded by several factors, including size, clarity, and crystal structure. Higher-quality diamonds are more resistant to breaking down under the stresses of polishing, which means they last longer and provide a finer finish. Durability testing often includes evaluating the quality of the diamond particles embedded in the pad, checking to see how well they hold up over time, and whether they continue to cut efficiently without dislodging too easily.
The type of bonding material used to hold the diamonds in place also plays a crucial role in the pad’s longevity. A poorly chosen binder can cause the diamonds to detach prematurely, significantly shortening the pad’s usable life. As such, durability testing also looks at the bonding materials to ensure they are strong enough to withstand the forces exerted during polishing while maintaining flexibility and resilience.
In real-world applications, the cost of replacing diamond polishing pads frequently can add up quickly, making it essential for professionals to choose pads that provide both quality and longevity. Durability testing helps to eliminate guesswork from this process, offering concrete data that allows users to select the best pads for their specific needs. Manufacturers, in turn, can refine their products to ensure they meet the highest standards of performance and reliability.
At the end of the day, durability testing is more than just a routine check. It’s a fundamental part of the process that ensures diamond polishing pads live up to their promise of offering exceptional performance over time. With the right testing protocols in place, both manufacturers and end-users can be confident that their investment in diamond polishing pads will result in smoother finishes, greater efficiency, and fewer replacements in the long run.
The role of durability testing in the world of diamond polishing pads cannot be overstated. It’s the key to understanding how these pads will perform in the real world, where consistency, quality, and longevity are non-negotiable.
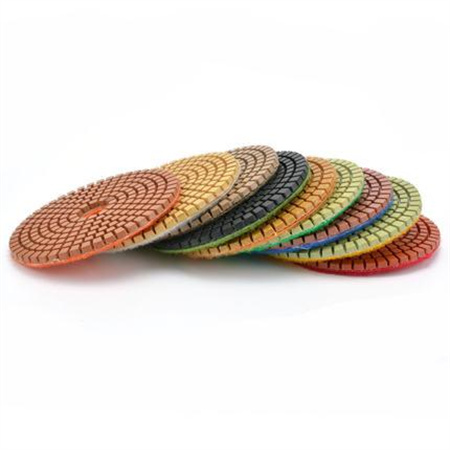