The Role of Resin in High-Performance Diamond Pads
In the world of precision grinding and polishing, diamond pads are often the go-to solution for achieving high-quality finishes on hard materials. Whether it’s in the semiconductor industry, automotive manufacturing, or even the production of fine glass, these pads play a crucial role in shaping surfaces to a mirror-like perfection. While the diamonds themselves are undoubtedly the stars of the show, the resin used to bond them is the unsung hero of high-performance diamond pads. Understanding the role resin plays can provide insights into why these pads are so effective and durable, offering the perfect balance of cutting power and finishing precision.
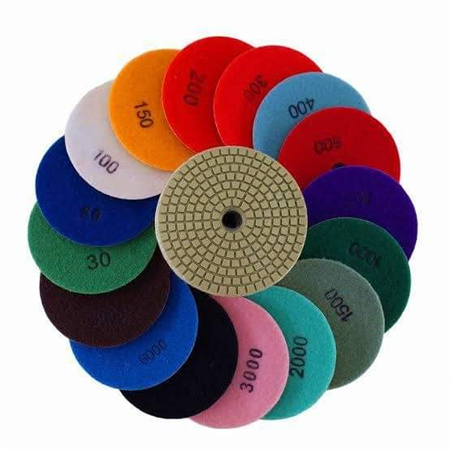
One of the primary roles of resin in diamond pads is to regulate the release of diamonds during the grinding or polishing process. Unlike metal-bonded pads, where the diamonds are embedded more firmly, resin-bonded pads allow the diamonds to wear out gradually and evenly. This controlled exposure of new diamond particles ensures that the pad remains aggressive enough to remove material without becoming overly abrasive, preventing the risk of damaging the workpiece. The uniformity with which diamonds are exposed during the wear cycle is key to maintaining a consistent finish, making resin-bonded pads ideal for high-precision applications.
The flexibility of resin also contributes to its effectiveness in high-performance diamond pads. Resin bonds tend to have a certain level of elasticity, which allows them to absorb shocks and distribute the pressure applied during grinding or polishing. This flexibility means that the pad can adapt to the contours of the workpiece more easily, leading to a smoother, more even finish. In applications where intricate shapes or delicate materials are involved, the resin’s ability to provide controlled pressure distribution is essential for achieving high-quality results.
Temperature resistance is another area where resin proves to be invaluable. When diamond pads are used in high-speed grinding or polishing processes, friction can generate significant amounts of heat. The resin must be able to withstand these temperatures without degrading, as any failure in the bond could result in the diamonds becoming dislodged or unevenly exposed, compromising the pad’s performance. High-performance resins are specifically designed to resist thermal degradation, maintaining the structural integrity of the pad even under extreme conditions. This heat resistance ensures that the pads can perform consistently, even during extended operations, without losing their cutting or polishing effectiveness.
The type of resin used in diamond pads also impacts the overall hardness and durability of the pad. Different formulations of resins are available, ranging from softer options that are ideal for more delicate finishing tasks to harder resins that are better suited for heavy grinding operations. The choice of resin can influence not only the lifespan of the diamond pad but also the surface finish it produces. Softer resins, for instance, are often chosen for applications requiring a finer finish, while harder resins are favored for their ability to sustain aggressive grinding over longer periods of time. Manufacturers carefully select the resin type based on the specific needs of the task at hand, ensuring the ideal balance between cutting power and finishing quality.
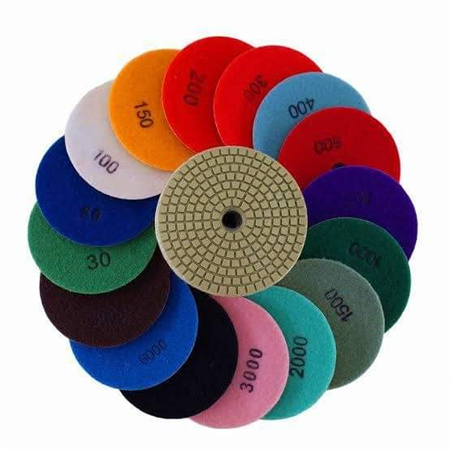
Resin also plays a key role in the environmental sustainability of diamond pads. Because resin-bonded pads are less likely to cause excessive wear or damage to both the material being worked on and the pad itself, they contribute to reducing waste. In comparison to other materials that might need to be replaced more frequently, resin pads often offer longer life cycles, which in turn helps reduce the need for frequent replacements and decreases overall material consumption.
When it comes to high-performance diamond pads, resin does far more than just hold the diamonds in place. Its role as a versatile bonding agent that helps regulate the release of diamonds, offers temperature resistance, provides flexibility, and influences hardness makes it an indispensable component. Whether you’re looking to achieve a fine finish on a delicate material or tackle heavy-duty grinding tasks, the right resin can make all the difference in the performance and longevity of your diamond pads. By choosing high-quality resin, manufacturers can ensure that their diamond pads continue to deliver exceptional results, consistently meeting the rigorous demands of precision industries.
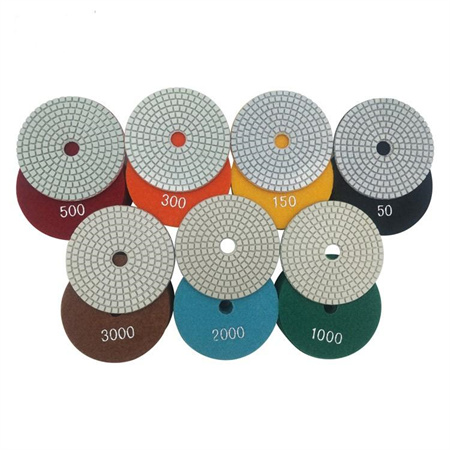