How to Evaluate Samples from a Polishing Pad Manufacturer
When selecting the right polishing pad for your needs, evaluating samples from a manufacturer is a crucial step. Whether you’re in the automotive, industrial, or furniture industry, the quality of your polishing pad can significantly impact the final product’s appearance and finish. To ensure you’re making an informed decision, it’s essential to assess the samples properly. Here’s how to evaluate samples from a polishing pad manufacturer effectively.
One of the first things to consider is the material used in the pad. Polishing pads come in various materials such as foam, microfiber, wool, or even a hybrid combination of these. Each material offers distinct advantages depending on the task at hand. For example, foam pads are often used for fine polishing, while wool pads are preferred for heavy-duty polishing. Understanding the material composition helps you align the pad with the requirements of your specific polishing job.
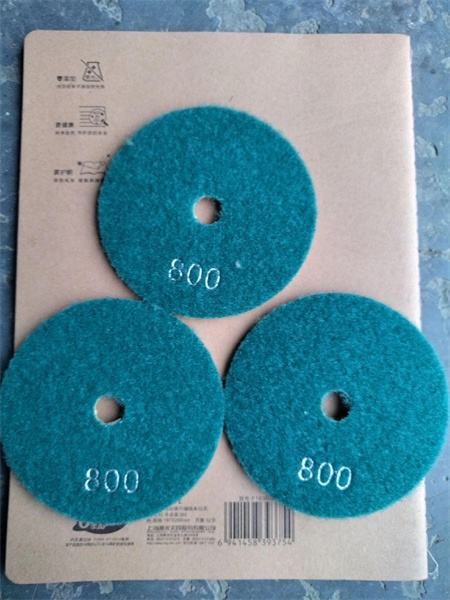
Another important factor is the pad’s ability to maintain a consistent level of performance. When polishing, you want to achieve a uniform finish, and this largely depends on the consistency of the pad’s performance. Test the sample on various surfaces, such as metals, painted surfaces, or composites, and observe how evenly it spreads the polishing compound. A pad that doesn’t wear down evenly can create inconsistencies in the finish, leading to blotches or uneven gloss levels.
The flexibility of the pad is another key aspect that should not be overlooked. Different surfaces require different levels of flexibility from a polishing pad. For example, if you’re polishing curved or irregularly shaped surfaces, you’ll need a pad that can adapt to the contours of the object without losing its effectiveness. A highly flexible pad allows for better coverage on complex shapes, reducing the risk of leaving streaks or unpolished areas. Testing this flexibility is as simple as applying the sample to a few objects with varying shapes and noting how well the pad conforms to the surfaces.
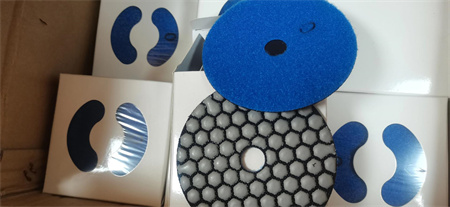
Another point of evaluation is the heat resistance of the polishing pad. When polishing at high speeds, friction generates heat, and pads that aren’t designed to handle high temperatures can break down or lose their performance. Some pads may even begin to melt or discolor when exposed to excessive heat. It’s important to determine whether the sample you’re testing can withstand these conditions without degradation. Pads with better heat resistance will be more reliable and long-lasting.
Noise and vibration are also worth considering, especially if you’re using the pad for extended periods or in environments where noise levels need to be kept low. Test the pad under real operating conditions and observe the sound levels. Excessive noise can not only be irritating but also a sign of poor quality materials or construction. Additionally, excessive vibrations can impact the quality of the finish and cause unnecessary strain on the operator.
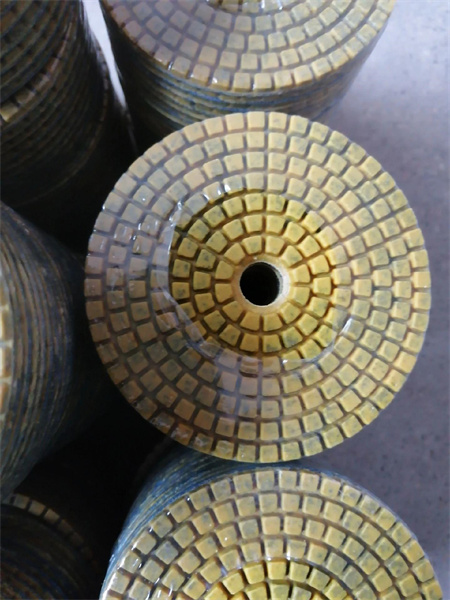
By carefully evaluating these factors—material composition, durability, performance consistency, flexibility, ease of use, heat resistance, noise and vibration levels, and cost-effectiveness—you can confidently choose the right polishing pad for your needs. Remember, a good polishing pad can save you time and effort, while a poor one can lead to additional costs and frustration. Take your time with the evaluation process, and you’ll end up with a product that meets your standards and helps you achieve that perfect finish every time.