Why Bond Type Matters in Diamond Pad Applications
In the world of precision grinding and polishing, diamond pads are crucial tools for achieving high-quality finishes on a range of materials, from metals to ceramics. While the diamonds themselves are often the star of the show due to their unparalleled hardness and sharpness, the bond type that holds these diamonds in place is just as important—perhaps even more so than many realize. Understanding why bond type matters can help manufacturers, engineers, and technicians select the right diamond pad for their specific application, optimizing performance and results.
At the heart of any diamond pad is the bond, the material that secures the diamonds to the pad’s surface. The bond type affects everything from how the diamond particles are released during grinding or polishing, to how the pad interacts with the workpiece and maintains its effectiveness over time. Bond types are typically categorized as metal, resin, ceramic, and electroplated, and each one brings distinct benefits and challenges.
Take metal bonds, for instance. These bonds are known for their strength and durability. Metal-bonded diamond pads are highly resistant to wear and tear, making them ideal for heavy-duty applications where long-lasting performance is crucial. However, because the bond is harder, it tends to release diamonds more slowly, which means the pads may not provide as aggressive a cut as resin bonds. But for operations that require consistent performance over a long period, like grinding concrete or polishing hard metals, metal-bonded pads can offer a level of stability and longevity that other bond types simply can’t match.
On the other end of the spectrum, resin bonds are softer and more flexible. Resin-bonded pads are popular for applications that require finer finishes and faster material removal. These pads are especially favored in industries like semiconductor manufacturing or the production of optical lenses, where precision is paramount. The softer resin bond allows for quicker diamond exposure, delivering a more aggressive cut at the start of the process. However, the trade-off is that resin bonds wear down faster than metal bonds, which means they may need to be replaced more often—something to consider if the application involves high-volume work or extended use.
Ceramic bonds represent a middle ground between metal and resin bonds, offering a blend of strength, durability, and flexibility. Ceramic-bonded diamond pads can provide consistent cutting action with less wear than resin bonds, while also offering a more controlled release of diamond particles than metal bonds. This makes ceramic bonds an appealing option for applications requiring a balance between speed and finish quality, such as the precision grinding of ceramics or the production of high-performance automotive components.
Electroplated bonds are another option, known for their ability to hold diamonds in a very precise manner. Electroplating involves the deposition of a thin layer of metal onto the pad, creating a rigid bond that holds the diamonds firmly in place. These pads are typically used in very specific, high-precision applications such as shaping or profiling hard materials. They provide excellent control and minimal wear, making them ideal for fine-tuned processes. However, the rigidity of the electroplated bond also means that the diamonds are released more slowly, limiting their aggressiveness compared to resin or metal bonds.
Choosing the right bond type for a diamond pad depends heavily on the specific requirements of the application at hand. Factors such as the hardness of the material being worked on, the desired surface finish, the operating conditions (e.g., wet vs. dry grinding), and the required lifespan of the pad all play into the decision. For example, if you’re working with a material that is relatively soft and requires a smooth finish, a resin bond might be the ideal choice. On the other hand, for harder materials or applications demanding longer tool life, a metal bond could be the better option.
In addition to material considerations, the bond type also influences the heat dissipation properties of the pad. Metal-bonded pads, with their high thermal conductivity, help to dissipate heat efficiently, which can prevent overheating during intensive grinding or polishing sessions. Resin bonds, by contrast, can trap more heat, which can lead to thermal degradation of both the pad and the workpiece if not carefully managed. This aspect is particularly important in applications like high-precision metalworking, where excessive heat can distort the material being processed or cause premature wear on the pad.
Ultimately, the bond type is not just a technical specification—it’s a critical factor in determining how well a diamond pad will perform in real-world conditions. The wrong bond type can lead to inefficiency, poor surface finishes, or premature tool failure, all of which can add cost and downtime to an operation. By carefully selecting the appropriate bond type based on the needs of the job, manufacturers can ensure that their diamond pads provide optimal performance and longevity, leading to better results and higher productivity.
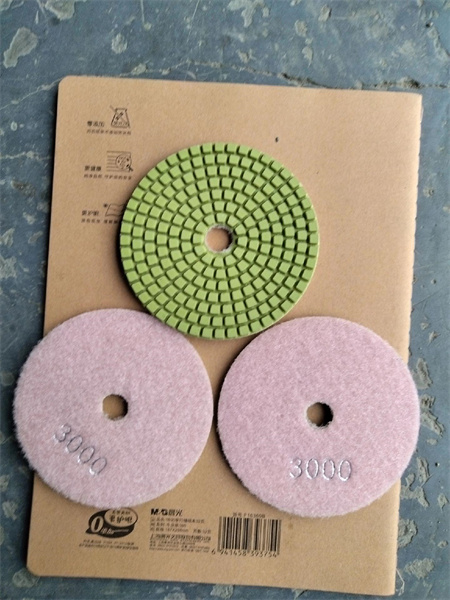