Key Considerations When Selecting Polishing Pads for Construction
When it comes to construction and renovation projects, the choice of polishing pads can significantly impact the quality of your work. Polishing pads are essential tools for achieving a smooth, professional finish on various surfaces, and making the right choice can enhance both efficiency and results. Here’s a detailed guide to help you navigate the crucial considerations when selecting polishing pads, tailored specifically for those in the construction industry.
1. Understand the Material of the Surface
Different surfaces require different types of polishing pads. For instance, diamond polishing pads are renowned for their ability to handle tough materials like granite, marble, and concrete. They are equipped with industrial-grade diamonds that provide a superior finish and durability. On the other hand, if you are working with softer materials, such as certain types of wood or softer stones, you might opt for polishing pads designed for those specific surfaces. Understanding the material you’re working with is the first step in selecting the right pad.
2. Grain Size and Grit Levels
The grain size of polishing pads determines how aggressive the pad will be. Grit levels typically range from coarse to fine. Coarse grit pads are ideal for heavy-duty work where you need to remove substantial amounts of material or deal with rough surfaces. Fine grit pads, however, are used for achieving a smooth, glossy finish. It’s important to choose the right grit level for the specific stage of your polishing process.
3. Pad Density and Flexibility
The density of the polishing pad affects its performance and lifespan. Higher density pads are more durable and suitable for heavy use, whereas lower density pads are more flexible and conform better to irregular surfaces. For example, a dense pad might be preferable for polishing large, flat areas, while a flexible pad could be better for detailed work on curved or uneven surfaces. Selecting the right density based on your project needs will ensure better results and longevity of the pads.
4. Backing Material
Polishing pads come with different backing materials, such as hook-and-loop, PSA (Pressure Sensitive Adhesive), or velcro. Each type of backing offers different advantages. Hook-and-loop backs provide easy attachment and removal, making them ideal for quick changes during a job. PSA backings offer strong adhesion and are often used for heavy-duty applications. The choice of backing material will depend on the specific requirements of your project and the equipment you’re using.
5. Compatibility with Equipment
Not all polishing pads are compatible with every polishing machine. Ensure that the pad you choose matches the specifications of your equipment, whether it’s a hand-held grinder, floor buffer, or another type of polishing machine. Proper compatibility ensures optimal performance and reduces the risk of damage to both the pad and the machine.
6. Durability and Longevity
Polishing pads vary in terms of durability. Diamond pads, for instance, are known for their exceptional longevity, making them a cost-effective choice for extensive projects. On the other hand, other types of pads may wear out more quickly, especially under heavy use. Evaluating the expected lifespan of a pad in relation to your project requirements will help you make an informed decision.
7. Cost vs. Quality
While it might be tempting to opt for the cheapest option available, it’s important to consider the balance between cost and quality. Higher-quality pads, such as those made with premium diamonds or advanced materials, often provide better results and longer lifespan, which can lead to cost savings in the long run. Assessing your budget in relation to the performance and durability of the pads will help you choose the best option for your needs.
8. Brand and Manufacturer
Choosing a reputable manufacturer can make a significant difference in the performance and reliability of your polishing pads. Established brands often have stringent quality controls and offer products that meet high standards. Researching and selecting pads from well-regarded manufacturers can ensure you receive a product that performs well and meets your expectations.
9. Environmental Considerations
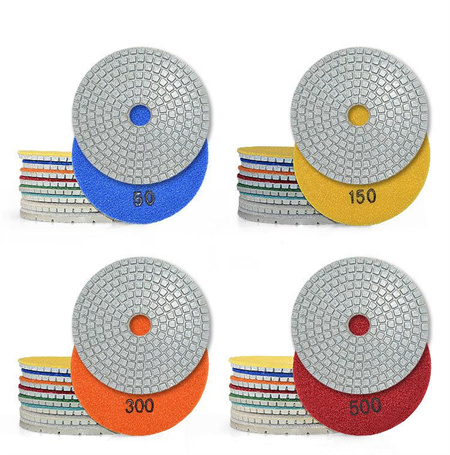
10. Specific Applications
Different polishing pads are designed for specific applications. For example, pads designed for concrete polishing will have different characteristics compared to those used for granite or marble. Consider the specific application of your polishing pad to ensure it’s tailored to the material and finish you’re aiming for.
In conclusion, selecting the right polishing pad involves a thorough understanding of your project requirements, the material you are working with, and the characteristics of different pads. By considering these key factors, you can ensure that you choose a pad that enhances your efficiency and delivers the high-quality results you’re aiming for. Whether you’re working on large-scale construction projects or smaller renovation tasks, making an informed choice will set you up for success.