Advanced Polishing Techniques for Experienced Users
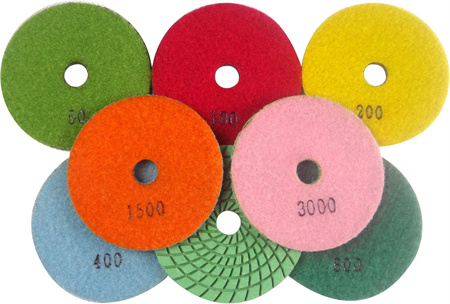
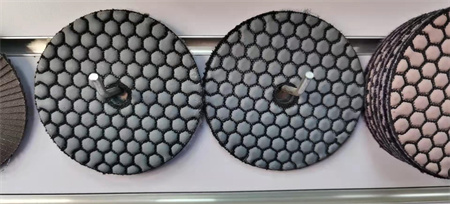
A critical component is the choice of abrasive. For those who’ve used standard polishing compounds, moving toward advanced formulations can make a significant difference. Fine-tuned abrasives, often designed for specific materials or applications, offer a higher degree of control and finer results. For instance, diamond abrasives are indispensable when polishing hard metals or gemstones. They allow for a smooth, consistent finish that would be impossible with traditional abrasives. Likewise, ceramic abrasives excel at polishing ceramics and composites, offering smoother surfaces without risking material damage.
The consistency and quality of the abrasive are just as important as the method of application. One common mistake made by even experienced users is underestimating the importance of working with the right consistency of the polishing compound. Too thick, and it won’t spread evenly; too thin, and it may wear out too quickly or fail to produce the desired finish. For those looking to achieve a mirror-like surface, balancing the application of compound thickness is crucial.
Speed plays a central role in achieving the perfect polish, yet it’s not as straightforward as simply cranking up the RPMs. The relationship between speed, pressure, and heat generation is delicate. High speeds generate heat, which can cause discoloration or warping of the material. Mastering the art of variable speed settings on your polishing machine can help manage this heat buildup while still allowing you to remove material efficiently. Slower speeds, on the other hand, give greater control and help refine finishes without overheating delicate surfaces.
In advanced polishing, the tool you use is just as important as the compound itself. Rotary and orbital polishers have different characteristics, each serving a unique function depending on the type of finish desired. Rotary polishers, for instance, are best for aggressive removal of material and are ideal when working with larger surfaces or tougher materials. However, they require more skill, as they can easily create swirl marks if not used properly.
Orbital polishers, on the other hand, are gentler and easier to use, particularly for achieving a high-gloss finish without damaging the material. They operate by creating a random orbital motion, which reduces the risk of creating marks on the surface. Skilled professionals often use a combination of both tools, depending on the stages of the polishing process.
Another advanced technique is wet polishing. By using water or specific lubricants during the polishing process, it’s possible to prevent overheating, reduce dust, and achieve a smoother finish. This technique is particularly useful when working with fragile materials such as glass or stone, where heat can cause cracks or unwanted blemishes. The water acts as a coolant, ensuring the abrasive particles remain effective without damaging the surface.
Polishing under controlled conditions—like using temperature-regulated environments or specialized lighting—can also have a significant impact on the final result. Lighting is one of the most overlooked elements in advanced polishing. The right lighting can reveal flaws or inconsistencies that may be invisible under normal conditions, giving you the opportunity to make last-minute adjustments. Whether you’re polishing a metal part to precision or perfecting the glass surface of a countertop, proper lighting helps ensure every detail is flawless.
A crucial yet often ignored detail in advanced polishing is the technique of “finessing” your work. Experienced users know that the finishing stages of polishing require the softest touch. Overworking a surface can lead to unnecessary wear and tear. As the finish becomes more refined, you need to work with lighter pressure and allow the polisher to gently buff the surface. It’s in these final stages where mastery truly shines, transforming what was once a rough surface into something practically flawless.
Advanced polishing is not just about the tools or materials—it’s about developing a deeper understanding of the interplay between every variable involved. As you gain experience, you’ll learn to read the surface you’re working on, adapting your technique to achieve that perfect finish. It’s this ability to finely tune your approach, adjust your equipment, and understand the material you’re working with that distinguishes a novice from an expert.
For those looking to go beyond standard polishing, embracing these advanced techniques will open up new dimensions of quality and precision. It’s about more than just finishing a project; it’s about mastering the art of making surfaces shine with expertise, control, and a meticulous eye for detail.
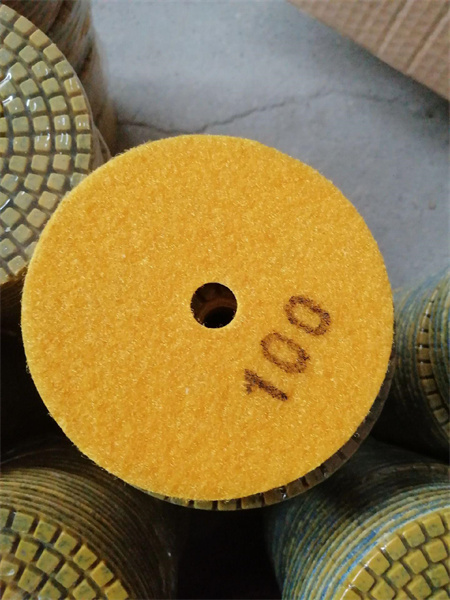