Reducing Operating Costs with Long-Lasting Polishing Pads
In any industry that involves machinery, metalworking, or surface finishing, the quest for efficiency is a constant priority. One of the most overlooked areas to achieve significant savings is through the use of high-quality, long-lasting polishing pads. These small but mighty tools can have a considerable impact on both the quality of the finished product and the bottom line of the business. By choosing durable polishing pads, manufacturers can minimize downtime, reduce waste, and, perhaps most importantly, cut operating costs.
The process of polishing, whether in automotive manufacturing, electronics, or metalworking, often requires specialized equipment and consumables. Polishing pads, typically made from foam, felt, or fabric materials, are crucial in achieving the smooth, flawless surfaces desired in finished products. However, their cost-effectiveness often gets lost in the rush for immediate results. While it’s tempting to purchase cheaper, lower-quality pads to reduce initial costs, the long-term impact on the operational budget can be much greater.
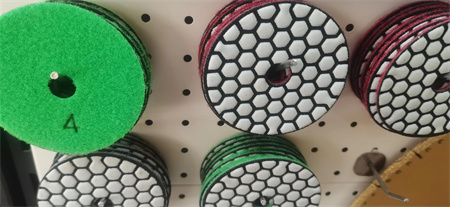
Another aspect to consider is the impact of polishing pads on the final product’s quality. Pads that wear down quickly tend to lose their effectiveness, leading to inconsistent finishes. This not only affects the aesthetics of the product but can also result in defects that require rework. The need for reprocessing not only wastes materials but also consumes valuable time and resources. Long-lasting pads maintain their performance for longer periods, ensuring that each product meets the required standards without the need for constant checks or touch-ups. This consistency helps reduce the occurrence of costly rework and ensures that production runs smoothly, with fewer errors.
Furthermore, high-quality pads are typically more efficient in terms of their polishing performance. They are designed to deliver more uniform pressure across the surface, preventing damage and reducing the amount of material lost during the process. In industries where precision is key, such as the automotive or aerospace sectors, even a small reduction in material loss can result in significant cost savings. Long-lasting pads also tend to produce fewer residues or contaminants, which can accumulate and degrade the finish. This translates to a cleaner work environment and less time spent on cleaning and maintenance tasks.
Another financial benefit of long-lasting polishing pads is their potential for reduced energy consumption. While it may seem indirect, the efficiency of the pads can impact the overall energy usage of the equipment. Pads that wear out quickly often require the machine to work harder to maintain the desired finish, leading to increased energy consumption. On the other hand, durable pads allow the equipment to operate at optimal levels without overexertion. This efficiency reduces the load on motors, cutting down on energy bills over time.
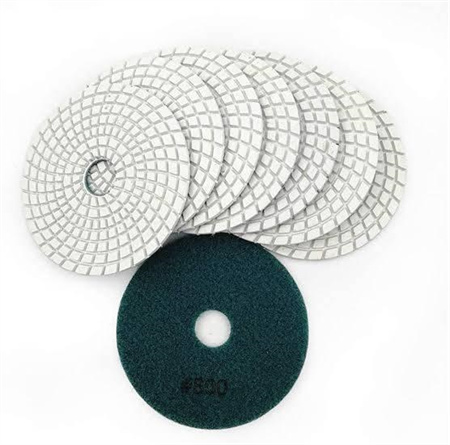
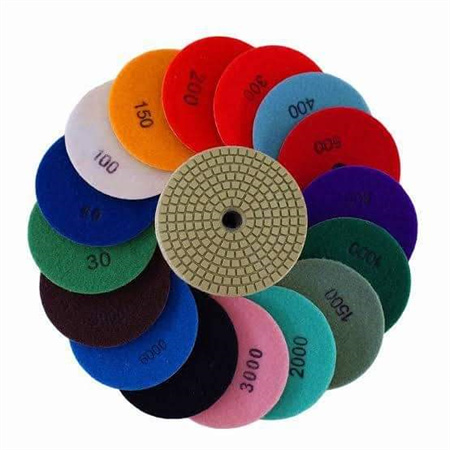
In conclusion, the true cost of polishing is not just the price of the consumables, but also the hidden costs associated with downtime, rework, material waste, and energy usage. By choosing long-lasting, high-quality polishing pads, businesses can make a smart investment that not only improves their operational efficiency but also lowers their overall operating costs. These pads provide a reliable and cost-effective solution to a common challenge in manufacturing and finishing industries, proving that sometimes, the best way to reduce costs is to invest in quality.