The Role of Pad Flexibility in Polishing Irregular Surfaces
When it comes to achieving the perfect finish on surfaces that are anything but flat, the role of pad flexibility cannot be overstated. Whether in industrial applications, automotive detailing, or even electronic device polishing, dealing with irregular surfaces presents a unique set of challenges. But it is precisely in these challenges where the magic of pad flexibility comes into play, making all the difference between a smooth, even finish and a product that requires constant rework.
At first glance, polishing might seem like a straightforward task – a matter of applying pressure, spinning a pad, and getting a glossy result. But for surfaces with bumps, curves, grooves, or other irregularities, the process becomes much more complex. Traditional, rigid pads might leave certain areas untouched or, worse, create uneven textures, resulting in a lackluster or flawed finish. That’s where the flexibility of the pad comes in.
Flexible pads are designed to adapt to the contours and variations of a surface. When polishing an irregular surface, these pads bend, stretch, and conform, ensuring that every inch of the surface is polished uniformly. This adaptability not only results in a smoother finish but also reduces the risk of damaging the material underneath. The key is how the pad’s flexibility allows it to follow the minute undulations of the surface, ensuring even pressure distribution and consistent contact.

One of the most significant benefits of using flexible pads is their ability to maintain consistent contact with the surface. Unlike rigid pads that can leave certain areas untouched if there are dips or edges, flexible pads can adjust to all these features, ensuring that every part of the surface gets the right treatment. This not only helps in polishing but also in preparing the surface for additional treatments like coating or painting. It ensures that the base layer is uniform, free of scratches, and ready for further processes.
Moreover, flexible pads can reduce the wear and tear on both the surface and the tool used for polishing. Rigid pads often require a bit more force to maintain contact with irregular surfaces, which can lead to over-polishing in some spots and under-polishing in others. A flexible pad, by contrast, requires less force while ensuring more comprehensive coverage. This can extend the life of both the pad itself and the surface being worked on, making the entire polishing process more efficient and cost-effective in the long run.
The technology behind flexible pads has evolved significantly over the years. Modern flexible polishing pads are often made from advanced materials like foam or microfiber that offer a high degree of compliance without sacrificing durability. Some pads even feature a unique layer design that combines firmness with flexibility, allowing them to work on a wide range of surfaces with varying degrees of texture and curvature.
In high-precision industries, the flexibility of the pad also plays a vital role in minimizing defects and imperfections. For example, in the semiconductor industry, where the smoothness of surfaces is critical, flexible pads help in producing ultra-flat, damage-free surfaces necessary for sensitive components. This ability to polish in a controlled, even manner helps prevent issues like micro-scratches or uneven thickness, both of which could have significant implications for the functionality of the final product.
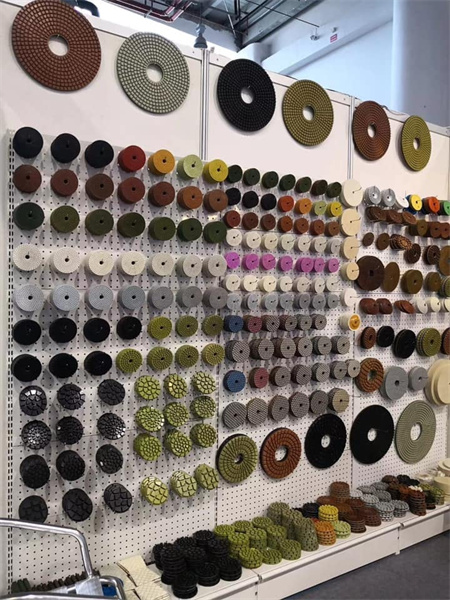
In conclusion, pad flexibility is a crucial factor when polishing irregular surfaces. It ensures consistent coverage, reduces the risk of damage, and enhances the overall quality of the finish. Whether in industrial manufacturing, automotive polishing, or even electronics, understanding the role of flexibility in polishing pads can lead to better results, longer-lasting products, and more efficient operations. The next time you tackle a challenging surface, remember: it’s not just about the right technique, but also about the right pad.
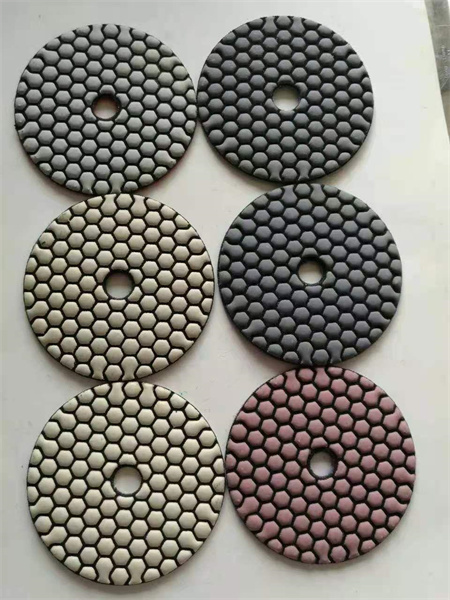