How We Compare to Global Competitors in Diamond Pad Quality
When it comes to diamond polishing pads, quality is everything. These tools are not just essential for achieving the perfect finish; they play a critical role in the longevity and effectiveness of various surfaces. So, how do we stand up against global competitors in the highly competitive world of diamond pad production?
At the heart of our approach lies a commitment to excellence. We understand that the quality of diamond pads doesn’t just depend on the raw materials but also on the technology and precision that goes into manufacturing them. Our pads are built to last longer, perform better, and meet the most demanding standards in industries ranging from stone and concrete polishing to glass and metal finishing.
Let’s take a closer look at how we measure up against the competition on the global stage.
Superior Material Quality
One of the key factors that set our diamond pads apart is the quality of the diamonds themselves. Unlike many global competitors who may opt for lower-grade diamonds to cut costs, we use only the finest, industrial-grade diamonds that ensure a more consistent finish and longer-lasting performance. The diamond quality is essential not only for effective polishing but also for avoiding premature wear and tear, which can be a common problem in pads made with inferior materials.
This attention to detail allows our pads to outperform others in terms of cutting speed and durability, even in tough conditions. Whether you’re working with granite, marble, or concrete, you can count on our pads to deliver superior results that you might not always get from other manufacturers.
Innovative Bonding Technology
The bonding of diamonds to the pad matrix is another area where we excel. Many competitors still rely on older, less effective bonding methods, which can result in uneven wear patterns and reduced performance over time. Our proprietary bonding technology ensures that the diamonds stay firmly in place, providing a consistent polishing action and preventing premature loss of material. This innovation leads to a smoother and more efficient polishing experience, even when used on high-stress jobs.
Our bonding process also takes into account the specific material and application the pads will be used for. Unlike some global brands that offer a one-size-fits-all solution, we customize our pads to meet the unique needs of various industries. This allows our customers to achieve the best possible results, no matter the challenge at hand.
Precision Manufacturing
Precision is at the core of our manufacturing process. We use state-of-the-art equipment to ensure each diamond pad is crafted to the highest standards. This means no more uneven edges, subpar finishes, or inconsistencies that can slow down your work and increase costs. While many competitors cut corners in the production process, we take the time to ensure that each pad is rigorously tested for quality and performance before it leaves our facility.
This level of precision doesn’t just make our pads better; it makes them more reliable. Consistency is crucial when it comes to diamond pads, and our commitment to accuracy means you can trust our products to deliver the same exceptional results every time.
Tailored Solutions for Every Need
One of the challenges with global competitors is their tendency to mass-produce products that may not always meet the specific needs of different markets. While some brands might offer a wide range of pads, they often lack the customizability or expertise to cater to particular requirements. We pride ourselves on offering tailored solutions that are designed to meet the exact specifications of each client.
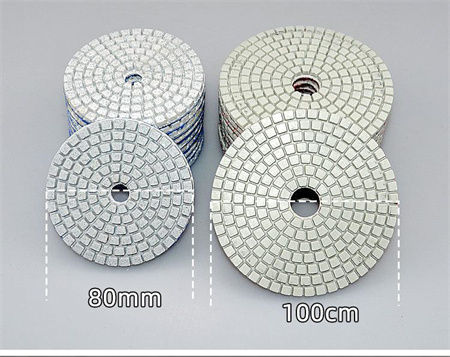
Customer Service and Support
While our product quality speaks for itself, we also believe that great customer service is a key differentiator. Many global competitors may provide a great product, but when it comes to after-sales support, they fall short. We make it a point to be available to our customers whenever they need assistance—whether it’s troubleshooting, offering advice on the best pad for a particular project, or providing timely replacements.
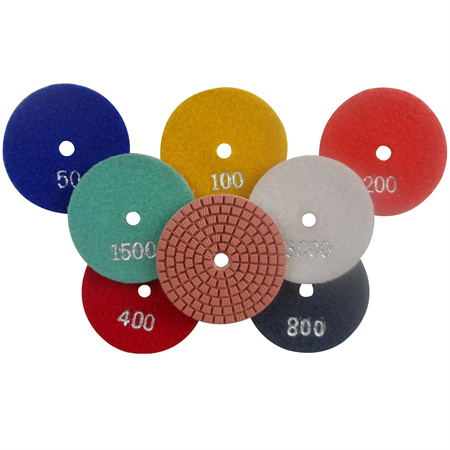
Sustainability and Ethical Practices
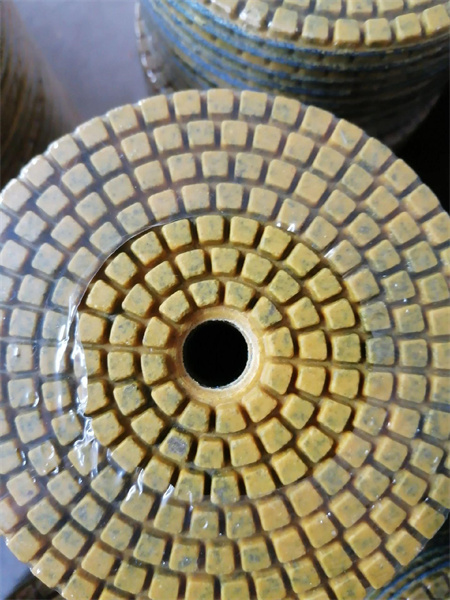
By choosing us, you’re not just opting for top-tier diamond pads; you’re also supporting a brand that’s conscious of its impact on the environment and dedicated to ethical business practices.
Final Thoughts
When you compare our diamond pads to those offered by global competitors, it’s clear that we go above and beyond in every aspect of design, production, and customer care. From superior materials and innovative bonding techniques to precise manufacturing and tailored solutions, we deliver products that stand out in terms of performance and reliability.
In the competitive world of diamond pads, we’re not just another brand—we’re the brand that ensures quality, consistency, and customer satisfaction every step of the way.