Reducing Environmental Impact During Diamond Pad Manufacturing
The diamond pad manufacturing industry plays a pivotal role in the world of high-precision polishing, especially in semiconductor and electronics manufacturing. However, the process of creating these essential tools can come with significant environmental challenges. From the extraction of raw materials to the energy-intensive production processes, diamond pad manufacturing often leaves a hefty carbon footprint. In recent years, companies have begun rethinking their approaches, pushing for greener, more sustainable practices. This shift is crucial not only for meeting industry regulations but also for reducing environmental harm and contributing to global sustainability goals.
One of the first areas where environmental impact can be mitigated is in the sourcing of materials. Traditional diamond pads are crafted from natural diamonds, which require extensive mining operations, causing environmental degradation, habitat destruction, and significant carbon emissions. A growing movement toward synthetic diamonds offers a promising alternative. Created in labs through processes like chemical vapor deposition (CVD) or high-pressure, high-temperature (HPHT) methods, synthetic diamonds can be produced with fewer resources and a smaller ecological footprint. This transition not only alleviates the environmental burdens of diamond mining but also ensures a more controlled and predictable supply chain.
Furthermore, manufacturers are focusing on improving the efficiency of the production process itself. Diamond pad manufacturing involves intricate processes such as bonding diamonds to a backing material, shaping the pads, and ensuring that the final product meets strict standards for precision. Many of these steps have traditionally been resource-heavy, requiring high amounts of energy, water, and chemicals. To combat this, manufacturers are adopting energy-efficient machinery and reducing water consumption by implementing closed-loop systems. These systems recycle water throughout the production stages, minimizing waste and ensuring that harmful chemicals do not contaminate local water sources.
One of the most exciting developments in diamond pad manufacturing is the use of sustainable binders and adhesives. Traditionally, the bonding agents used in the process have been based on petroleum-derived chemicals, which contribute to pollution and are not biodegradable. By shifting to bio-based adhesives and environmentally friendly bonding materials, manufacturers are cutting down on the use of toxic substances and reducing their reliance on fossil fuels. This not only makes the pads safer to handle but also decreases their overall environmental impact.
At the same time, manufacturers are embracing a circular economy approach, where the end-of-life phase of diamond pads is carefully considered. Rather than discarding used pads, companies are now exploring ways to repurpose or recycle them. For example, worn-out pads can be reconditioned by removing the old diamond particles and adding new ones, giving the product a second life. In some cases, the materials used in the pads are fully recyclable, which further minimizes waste and supports the long-term sustainability of the manufacturing industry.
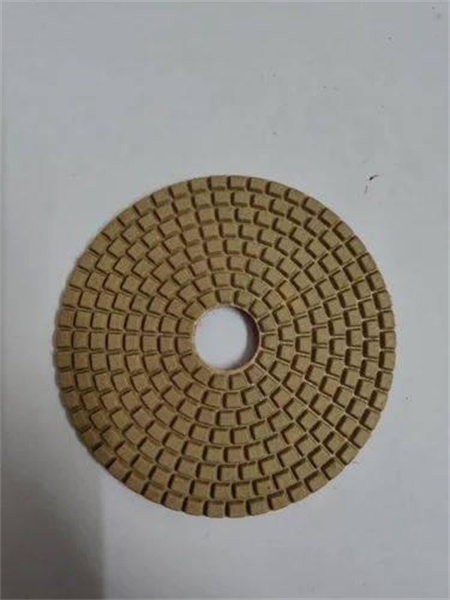
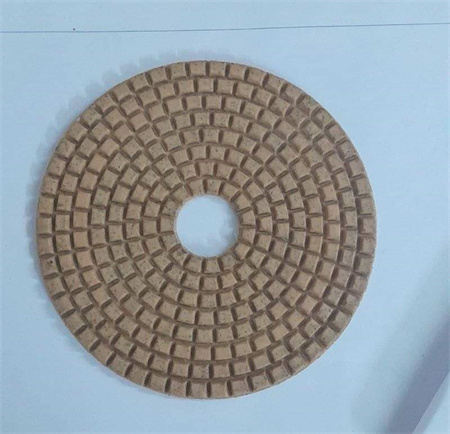
The importance of these changes cannot be overstated. As consumers and businesses alike become more aware of the environmental challenges facing the world, there’s an increasing demand for products and practices that prioritize sustainability. For manufacturers of diamond pads, adopting these innovative, eco-friendly approaches is not just a trend—it’s a responsibility. By continuing to push for advancements in sustainable production methods, the industry is not only reducing its environmental footprint but also contributing to the broader global effort to combat climate change.
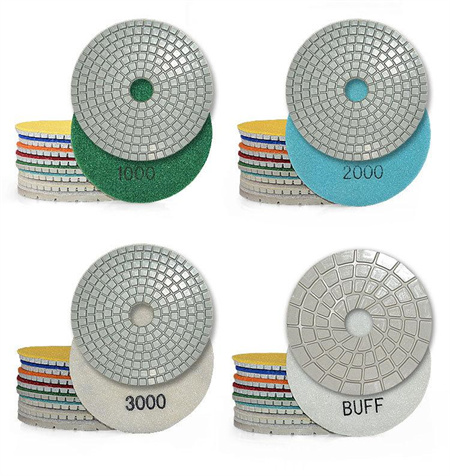