How Nanotechnology Could Improve Polishing Pad Durability
The world of manufacturing and precision engineering has long been focused on enhancing the performance and longevity of tools and components. Among the most critical parts of various industrial processes are polishing pads. These seemingly simple tools, used for finishing surfaces to a mirror-like smoothness, play a vital role in numerous industries, from automotive to electronics. However, as essential as polishing pads are, they often face challenges related to wear and tear, reducing their effectiveness over time. Enter nanotechnology, a field that promises to revolutionize not just the way we approach material science but also how we improve the durability and performance of polishing pads.
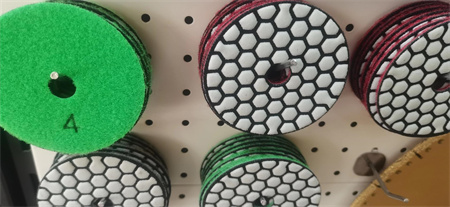
One of the key benefits of nanotechnology is its ability to enhance the physical properties of materials. By incorporating nanomaterials into the composition of polishing pads, manufacturers can significantly increase the pad’s resistance to wear. Traditional polishing pads are often made from a combination of polyurethane, foam, or felt, materials that wear down quickly under pressure and friction. Nanomaterials, such as carbon nanotubes, graphene, or silica nanoparticles, can be embedded into these materials to reinforce their structure, making them more resistant to abrasion and deformation.
The introduction of these tiny yet powerful materials at the nanoscale works by distributing stress more evenly across the pad’s surface. This results in a more uniform wear pattern, reducing the likelihood of premature degradation. As a result, polishing pads enhanced with nanotechnology can maintain their effectiveness for a longer period, even under the demanding conditions of high-speed polishing processes.
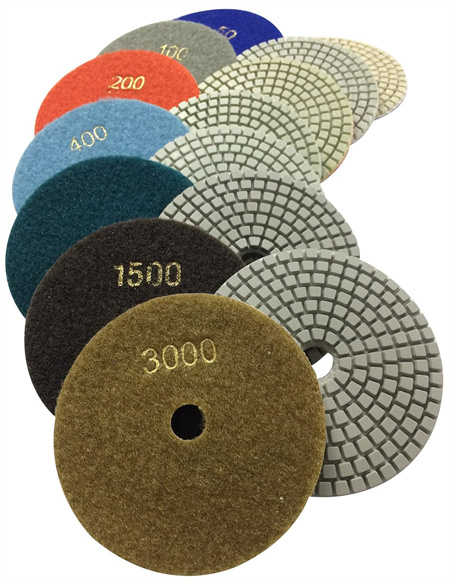
Another exciting possibility that nanotechnology offers is the ability to create self-healing polishing pads. This concept, while still in its developmental stages, could be a game-changer. By incorporating nanoparticles that respond to damage, polishing pads could potentially “repair” themselves when small cracks or wear patterns appear. The self-healing process would be akin to how certain materials can regenerate after being subjected to stress, reducing the need for constant replacements and repairs. For industries relying on polishing pads for continuous production, such a development could mean massive savings in both time and resources.
Beyond durability, nanotechnology also holds the potential to improve the efficiency of polishing pads. Nanocoatings, for example, can be applied to the surface of polishing pads to create ultra-smooth finishes that reduce friction during use. These coatings can also be engineered to resist contaminants, such as dust or oils, that often compromise the polishing process. With a cleaner, smoother surface, the pad can perform more effectively, delivering better results with less effort. This is especially important in high-precision industries like semiconductor manufacturing, where even the slightest imperfection in the polishing process can lead to defects in the final product.
Environmental considerations are also driving the interest in nanotechnology for polishing pad development. By using more durable and efficient materials, manufacturers can reduce waste associated with frequent pad replacements. Additionally, nanomaterials can be designed to be more eco-friendly, further supporting the trend toward sustainable manufacturing practices. The ability to extend the lifespan of polishing pads means fewer pads are required, and less material is consumed in the long run, benefiting both the environment and the bottom line.
The potential of nanotechnology in enhancing polishing pad durability is not just a futuristic concept—it’s happening now. With ongoing advancements in nanomaterials and coatings, the possibilities for more durable, efficient, and sustainable polishing pads are becoming a reality. Industries that rely on these pads for their critical polishing processes can look forward to significant improvements in both cost-effectiveness and performance.
In conclusion, the intersection of nanotechnology and polishing pad design is poised to transform the way we think about tool longevity and efficiency. With stronger, more heat-resistant, and even self-healing pads on the horizon, nanotechnology offers an exciting avenue for innovation in the world of surface finishing. As manufacturers continue to push the boundaries of material science, polishing pads will no longer be viewed as expendable tools but as sophisticated, long-lasting components that help drive industrial excellence.
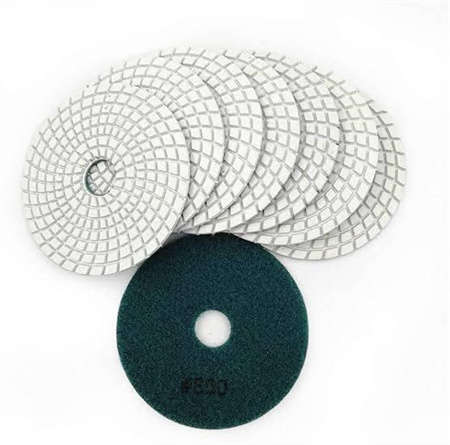