How to Reduce Water Waste During Wet Polishing
Wet polishing is a standard process used in industries like construction, stonework, and even some forms of metalworking, where water is applied to reduce heat and friction while polishing surfaces. However, the use of water in wet polishing often leads to significant waste, which can have negative environmental and financial impacts. Fortunately, there are effective strategies to minimize water waste during the wet polishing process. Here’s how you can make the most out of every drop while still achieving a smooth, high-quality finish.
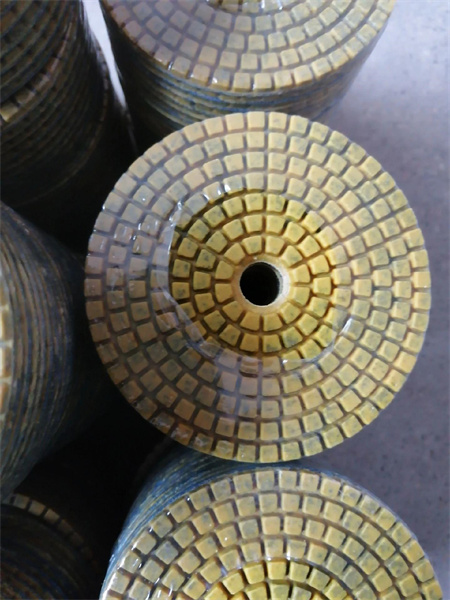
Another key factor in reducing water waste is proper maintenance of the polishing equipment. Over time, polishing pads, discs, and other components can become clogged with debris, which not only affects their performance but also leads to unnecessary water spillage. Keeping your equipment clean and well-maintained ensures that the water is being used effectively and efficiently. A clogged pad, for instance, may cause uneven polishing and require more water to cool down the surface, which could be avoided with proper care.
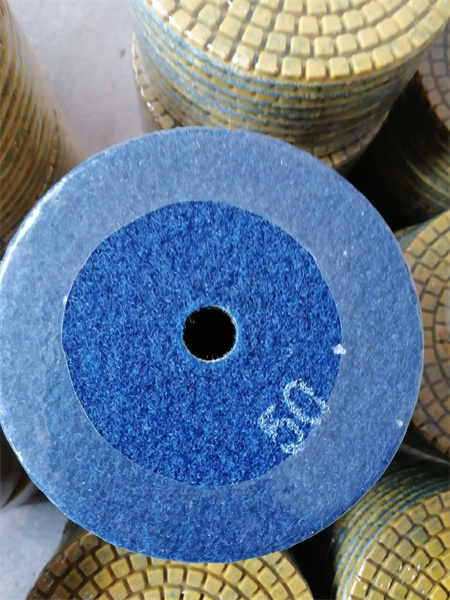
Water flow patterns also play a significant role in conservation. Consider using a more directed approach to applying water, rather than allowing it to flow freely over the workpiece. By using water delivery systems that apply water in a targeted manner, you can prevent excess from splashing or running off the edges. This approach also helps keep the workspace cleaner and prevents pooling, which can lead to slippery surfaces and safety hazards.
Sometimes, workers inadvertently waste water by simply not being mindful of how much is needed. Being conscious of the task at hand and knowing when to pause and reassess water usage can help avoid unnecessary overflow. For instance, instead of leaving the water running continuously, try using water only when the polishing action requires it. This practice can be especially beneficial when polishing smaller surfaces or in situations where the cooling effect of the water is needed intermittently.
In addition to conserving water, it’s worth considering the type of water being used. In many industrial settings, tap water is commonly used for wet polishing, but in certain cases, recycled water can be just as effective. Water treatment systems can be employed to filter and purify water for reuse, reducing the strain on local water supplies and cutting down on the costs associated with continuously sourcing fresh water.
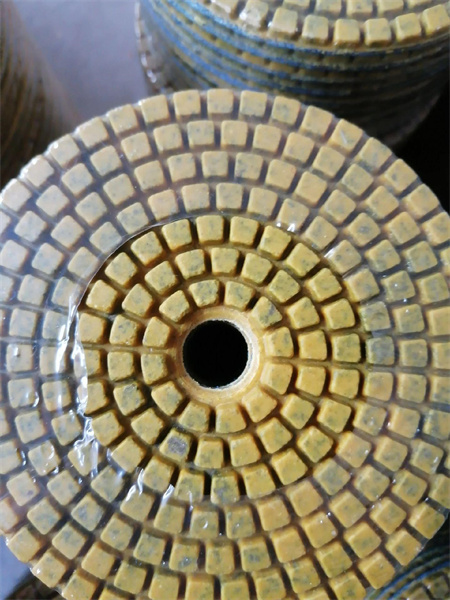
Lastly, consider how the byproducts of wet polishing are handled. Many wet polishing processes create slurry—a mixture of water, polishing compound, and debris. Proper disposal and management of slurry not only reduces waste but also prevents water contamination. By using eco-friendly disposal methods or recycling the slurry for use in other processes, you can further reduce environmental impact.
Water waste is an issue that affects industries worldwide, but with thoughtful adjustments and a bit of care, it’s possible to reduce consumption without compromising the quality of the work. By optimizing equipment, maintaining tools, rethinking workspace layouts, and fostering awareness among workers, you can significantly lower the amount of water used in wet polishing. These small changes can lead to big savings and a more sustainable, efficient polishing process.