Durability Testing of Diamond Polishing Pads
When it comes to achieving a flawless finish on various surfaces, diamond polishing pads are an essential tool in the toolkit of professionals across multiple industries. These pads are renowned for their exceptional durability and efficiency, making them a top choice for tasks ranging from concrete polishing to granite and marble maintenance. But how do we ensure that these pads meet the high standards expected by users? The answer lies in rigorous durability testing.
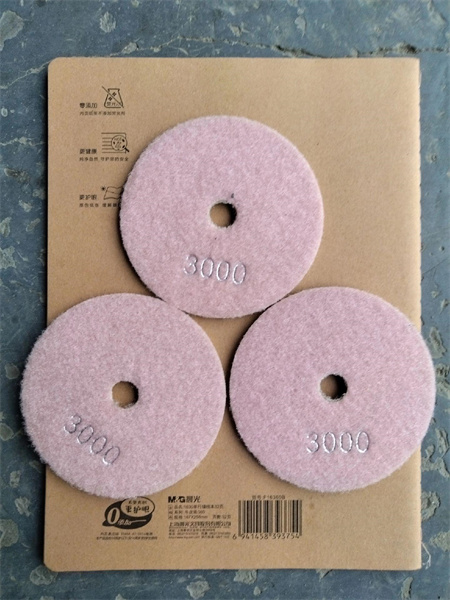
Diamond polishing pads are specifically engineered to handle the toughest of jobs. Their core advantage lies in the diamond particles embedded within the pads, which offer superior hardness and longevity compared to conventional abrasives. These pads are used in various applications, including floor grinding, surface preparation, and high-gloss finishing. Given their critical role, it’s crucial to test their durability to guarantee they perform reliably over time.
Why Durability Testing Matters
Durability testing of diamond polishing pads is not just a quality assurance step; it’s a necessity for ensuring that the pads can withstand the harsh conditions they will face in real-world applications. Testing helps in identifying any potential weaknesses in the pads’ construction, such as premature wear or failure under heavy use. This is particularly important for importers, wholesalers, and retailers who depend on the reliability of these products to satisfy their customers.
Key Aspects of Durability Testing
1. Wear Resistance: One of the primary tests conducted is assessing the wear resistance of the polishing pads. This involves simulating prolonged use under controlled conditions to measure how well the pads maintain their effectiveness over time. Pads are subjected to abrasive surfaces to gauge the rate of diamond loss and pad degradation.
2. Performance Under Extreme Conditions: Diamond polishing pads must perform consistently under various environmental conditions. Testing includes evaluating the pads’ performance under high temperatures, varying humidity levels, and different surface types. This ensures that the pads will deliver reliable results regardless of external factors.
3. Consistency and Quality Control: Each batch of polishing pads is subjected to stringent quality control measures to ensure consistency. This includes checking for uniform diamond distribution and the integrity of the bonding agent that holds the diamonds in place. Consistency in manufacturing is crucial for maintaining the performance standards expected by users.
4. Longevity Testing: Longevity tests simulate extended periods of use to determine how long the pads can maintain their efficiency. This involves continuous grinding or polishing processes to evaluate how the pads stand up to prolonged stress.
Key Benefits of Rigorous Durability Testing
1. Enhanced Reliability: By rigorously testing the durability of diamond polishing pads, manufacturers can ensure that their products are reliable and perform as expected. This reliability is crucial for professionals who depend on these tools for high-stakes projects.
2. Customer Satisfaction: High-quality, durable polishing pads lead to greater customer satisfaction. When users experience fewer issues with pad wear and tear, they are more likely to be satisfied with their purchase and continue using or recommending the product.
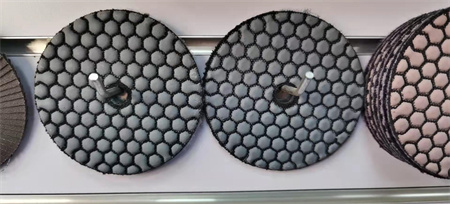
4. Competitive Advantage: In a competitive market, having a reputation for durable and reliable products can set a manufacturer apart from competitors. Effective durability testing demonstrates a commitment to quality, which can enhance a brand’s reputation and appeal.
Industry Applications and Keywords
Understanding the applications and keywords associated with diamond polishing pads helps in targeting the right audience. Common applications include concrete floor polishing, granite countertop finishing, and marble restoration. Relevant keywords for this industry include “diamond polishing pad manufacturer,” “wholesale diamond polishing pads,” “durability testing diamond pads,” and “diamond pads for concrete polishing.”
Importers, wholesalers, and retailers should be familiar with terms like “diamond abrasive pads,” “high-performance polishing pads,” and “durable polishing solutions.” These keywords can assist in optimizing online content and attracting the right customer base.
Conclusion
Durability testing is an indispensable part of the diamond polishing pad manufacturing process. It ensures that the pads are not only effective but also reliable over extended periods of use. For businesses involved in the distribution and retail of diamond polishing pads, understanding and emphasizing the results of these durability tests can significantly impact their success. By focusing on quality and performance, manufacturers can build trust with customers and establish a strong presence in the competitive market of diamond polishing solutions.